Industries that operate in high-dust environments face unique and often severe challenges, including managing airborne particles’ health and safety risks while adhering to strict environmental and safety regulations. Among these challenges, the danger posed by dust explosions remains one of the most significant threats to both personnel and infrastructure. These explosions can cause catastrophic damage, resulting in fatalities, operational shutdowns, and long-term reputational harm. Addressing such risks necessitates a blend of advanced engineering, strict regulatory compliance, and proactive safety measures integrated into dust collection systems.
This comprehensive guide delves into the causes of dust explosions, explores modern safety solutions, and highlights how Intensiv-Filter Himenviro sets the benchmark with cutting-edge systems that ensure workplace safety, operational efficiency, and compliance with international standards.
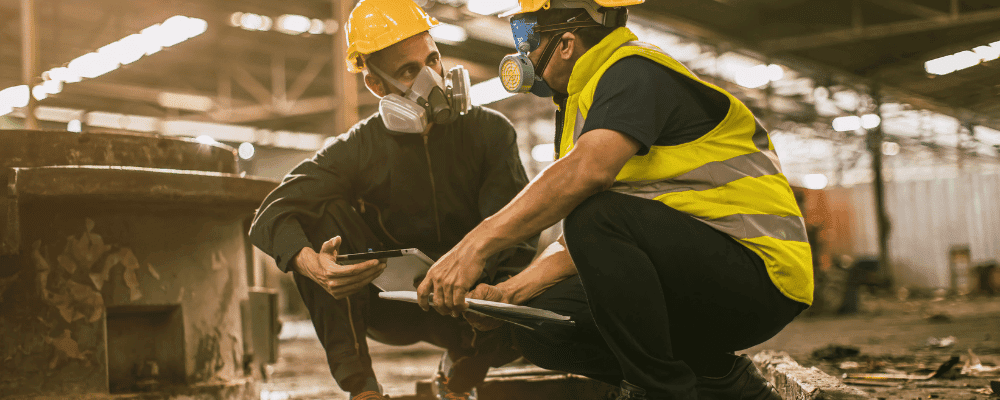
Kết nối với chúng tôi ngay
Understanding the Risk of Dust Explosions
The devastating nature of dust explosions underscores the need to understand their mechanics and causes fully. Fundamentally, a dust explosion occurs when a cloud of combustible dust ignites in an enclosed or semi-enclosed space, resulting in a rapid and violent combustion process. For this reaction to occur, five critical elements must align:
- Combustible Dust: Particles such as sawdust, sugar, coal, or metal powders.
- Oxygen: Naturally present in air and a necessary component of combustion.
- Ignition Source: This can be a spark, flame, or even static electricity. Dust Dispersion: Fine particles suspended in the air to create a combustible mixture.
- Confinement: Enclosed spaces like silos, ducts, or machinery can amplify the explosion’s impact.
Industries at Risk
Certain industries face heightened risks of dust explosions due to the type and quantity of dust generated in their operations. For instance, the woodworking industry deals with fine sawdust, which is highly flammable and easily dispersed in the air. Similarly, the food processing sector generates combustible dust from grains, sugar, and spices, while metalworking involves fine powders of aluminum and magnesium—both of which are highly volatile.
The pharmaceutical and chemical industries, where fine powders are commonplace, also experience significant risks. Moreover, in large-scale operations such as mining and cement manufacturing, the sheer quantity of dust produced exponentially increases the chances of explosions.
Real-Life Incidents
Several incidents have brought global attention to the catastrophic nature of dust explosions. The Imperial Sugar Refinery explosion in 2008 remains one of the deadliest cases, with 14 fatalities and extensive destruction. Investigations revealed that improper maintenance and excessive dust accumulation were major contributors.
Similarly, grain elevators, common in the agricultural sector, are notorious for dust explosions. The combination of fine dust particles, inadequate ventilation, and confined storage conditions often proves disastrous. These real-life examples underscore the importance of robust safety measures and advanced dust collection systems in mitigating risks.
How Dust Collection Systems Mitigate Risks
Dust collection systems serve as the frontline defense against the risks posed by airborne dust particles. These systems are designed to capture hazardous particles at their source, convey them to a safe collection point, and prevent their dispersion into the environment. However, without integrated safety features, these systems can inadvertently act as ignition sources, exacerbating the risks of dust explosions.
Core Functions of Dust Collection Systems
The primary functions of any dust collection system include capturing, conveying, containing, and controlling dust particles. At the heart of these operations are advanced mechanisms and safety measures tailored to specific industrial needs. For instance, capturing mechanisms remove airborne dust directly from the source, while conveying systems transport the collected dust to a central collection point. Containment solutions ensure the dust is stored safely, preventing its re-dispersion.
Modern dust collection systems, particularly those engineered by Intensiv-Filter Himenviro, go beyond these core functions by integrating advanced safety mechanisms that significantly reduce the likelihood of explosions.
Advanced Safety Features in Dust Collection Systems
Effective dust explosion prevention relies on the integration of advanced safety features within dust collection systems. Among these, explosion vents, isolation valves, spark arrestors, flameless venting systems, and inerting technologies stand out as critical components.
Explosion Vents
Explosion vents serve as essential pressure-relief mechanisms in the event of an explosion. When a dust explosion occurs, these vents channel the excess pressure to a safe area, preventing structural damage to equipment and facilities. Explosion vent designs vary to suit specific industrial needs, ranging from single-layer vents for basic applications to multi-layer vents designed for heavy-duty operations.
Flameless Venting Systems
While traditional explosion vents release pressure, they can also emit flames, posing significant risks in indoor environments. Flameless venting systems eliminate this risk by incorporating flame arrestors, which extinguish flames during the pressure release process. This technology is particularly beneficial in industries such as pharmaceuticals and food processing, where stringent indoor safety standards are required.
Isolation Valves
Isolation valves are another critical safety feature, preventing explosions from propagating through duct systems and reaching other areas of the facility. These valves come in two main types: mechanical valves that create a physical barrier and chemical isolation systems that neutralize explosions by injecting extinguishing agents.
Spark Arrestors
Spark arrestors intercept hot particles or sparks traveling through duct systems, stopping them from reaching combustible dust accumulations. These devices are especially important in industries like woodworking and metalworking, where sparks are common byproducts of operations.
Inerting Systems
Inerting systems address the risk of combustion by reducing the oxygen concentration within dust collectors to levels below the combustion threshold. These systems commonly use gases like nitrogen and carbon dioxide, making them ideal for applications in metalworking and chemical processing industries.
Khám phá các giải pháp của chúng tôi:
NFPA Compliance: The Gold Standard for Safety
Các National Fire Protection Association (NFPA) has developed detailed guidelines to mitigate the risks associated with dust explosions. Compliance with these standards improves workplace safety, ensures regulatory adherence, and reduces operational hazards. Prominent NFPA standards include:
- NFPA 652: Outlines procedures for conducting Dust Hazard Analyses (DHA).
- NFPA 68: Specifies methods for explosion venting.
- NFPA 69: Details explosion prevention measures.
- NFPA 654: Focuses on minimizing dust accumulation to lower ignition risks.
Compliance with these standards not only enhances workplace safety but also offers financial benefits, such as reduced insurance premiums and greater operational reliability.
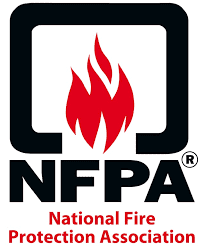
Intensiv-Filter Himenviro: A Leader in Dust Explosion Prevention
Intensiv-Filter Himenviro has established itself as a global leader in dust explosion prevention through its innovative, NFPA-compliant systems that prioritize safety, efficiency, and sustainability. The company offers holistic safety solutions by designing dust collection systems with integrated features such as explosion vents, flameless venting systems, isolation valves, and spark arrestors. These solutions are tailored to address the specific challenges of various industries, ensuring optimal performance and safety. With industry-specific expertise spanning sectors like woodworking, pharmaceuticals, food processing, metalworking, and cement manufacturing, Intensiv-Filter Himenviro delivers customized systems to meet diverse needs. For instance, their solutions manage high-temperature dust in cement plants, ensure contamination-free safety in pharmaceutical operations, and effectively capture fine sawdust in woodworking applications. Furthermore, the company emphasizes sustainability by incorporating energy-efficient designs and eco-friendly materials, aligning with global sustainability goals and enhancing long-term operational efficiency. To ensure peak performance, Intensiv-Filter Himenviro provides comprehensive lifecycle support, from installation to maintenance, solidifying its position as a trusted partner in high-dust industries.
Ứng dụng trong nhiều ngành công nghiệp
The versatility of Intensiv-Filter Himenviro’s systems enables them to address the unique challenges of various industries. For instance, in woodworking, the systems effectively manage the high fire risks posed by fine sawdust. In food processing, the company’s solutions prevent both fire hazards and contamination risks associated with dust from grains, sugar, and spices.
In pharmaceuticals, advanced monitoring systems detect hazards in real time, ensuring precision handling of fine powders. For metalworking, the company’s inerting systems and robust containment solutions are ideal for managing the explosive risks posed by aluminum and magnesium dust. Lastly, in the cement and mining sectors, heavy-duty systems designed by Intensiv-Filter Himenviro withstand harsh environments and high dust loads.
The Future of Dust Explosion Prevention
The future of dust explosion prevention lies in the integration of smart systems and sustainable practices. Innovations like IoT-enabled dust collection systems enable predictive maintenance and real-time monitoring, minimizing risks proactively.
Artificial intelligence is also playing a growing role in safety, dynamically adapting system responses based on real-time conditions. Additionally, the shift toward sustainable practices, such as energy-efficient designs and recyclable materials, aligns with global environmental goals and ensures long-term operational viability.
Phần kết luận
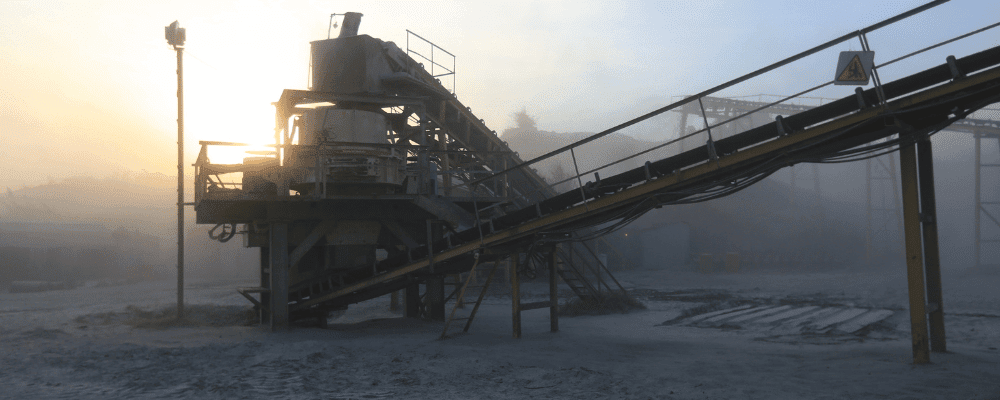
Dust explosions are preventable tragedies that demand a proactive and comprehensive approach. By integrating advanced safety features like explosion vents, spark arrestors, and isolation valves, modern dust collection systems can significantly mitigate risks.
Intensiv-Filter Himenviro, with its innovative, NFPA-compliant solutions, has established itself as a trusted leader in industrial safety. Through its commitment to engineering excellence, industry-specific expertise, and sustainability, the company ensures that its clients can operate safely and efficiently in even the most challenging environments. For industries seeking reliable and future-proof dust collection systems, Intensiv-Filter Himenviro remains the partner of choice.