The process filter ProJet mega have been developed for dedusting large volume flows. The variety of parts of the ProJet mega series is significantly reduced while maintaining a maximum number of possible explanations. For a relatively small number of constructive primitives are solely responsible for in-line filter of 1-12 filter chambers (each with 8 injector pipes x 8-17 injectors per row) represented over 600,000 different versions. This account of the different process engineering and structural conditions is supported, which are required for process filters.
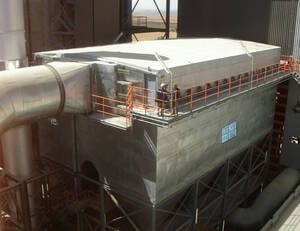
Bag filter series ProJet mega in 3D visualization showing details, procedures, processes and reactions within the filter system:http://www.youtube.com/user/IntensivFilter
Special Features of the process filter ProJet Mega
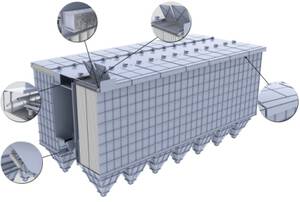
- Distribution of the raw gas through a CFD optimized flow control system
- CFD optimized design of clean- and raw gas valves with robust pneumatic actuator and minimal flow resistance
- Valve block with integrated membrane
- The latest Injector technology
- All online and offline modes of operation are implemented in the standard, e.g. semi-offline with low pressure cleaning, low air consumption, maximum tube life.
- Cleaning control means JetBus controller and residual pressure regulated control
- Reduced compressed air requirements
- Minimized load on the filter bags and increase of operating life
- Also Equipment with energy efficient ProTex filter media
Cleaning system for the Process Filter ProJet Mega
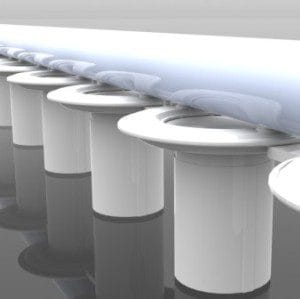
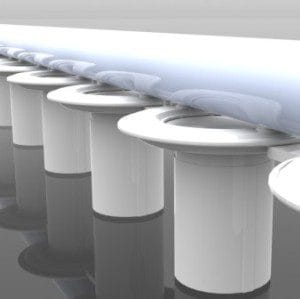
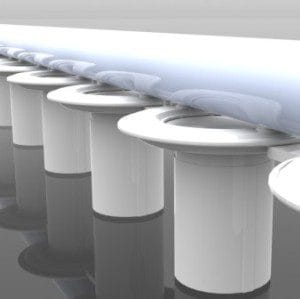
The cleaning control of the new process filter ProJet mega via microprocessor technology and fieldbus systems. Bộ lọc Intensiv Himenviro sets for a long time tested and patented JetBus controller that regulates the cleaning pressure. The timing of the pressure pulses is varied depending on the requirement. Optionally, a fixed timing, or a differential pressure control can be applied with variable cycle times.
Life Cycle Cost of the Process Filter ProJet Mega
In dedusting processes, as compared to conventional bag filters with the process filter ProJet mega substantial savings in energy costs can be achieved. With the same process conditions, a reduction of energy costs by 45% can be achieved. This result is achieved by the combined effect of the reduction of the filter resistance and compressed air requirement in the semi-offline mode, as well as by the lower differential pressure when using the ProTex PI filter medium. Since the maintenance, Filter media- and investment costs can be reduced to the newly developed filter technology, LCC, a record time of 10 years, be reduced by 40%
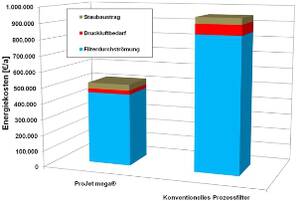
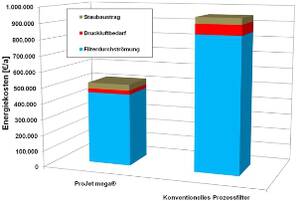
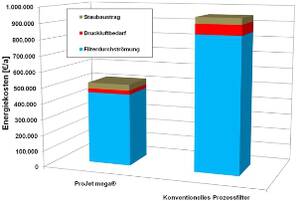