Did you know that sulfur dioxide (SO₂) emissions are one of the primary causes of acid rain? Industrial processes that burn fossil fuels—such as power plants, cement manufacturing, metal refining, and petrochemical industries—release vast amounts of SO₂ into the atmosphere. Without proper control measures, these emissions lead to severe environmental and health consequences, including respiratory diseases and ecological damage.
This is where Flue Gas Desulfurization (FGD) plays a crucial role. As a highly efficient pollution control technology, FGD removes sulfur dioxide from flue gases before they are released into the air. This significantly reduces environmental impact, helping industries comply with stringent emissions regulations and contributing to global sustainability goals.
But how does FGD work, and why is it increasingly essential for industries worldwide? Let’s dive deeper into the process, its significance, and its future in industrial air pollution control.
Understanding the FGD Process
Think of FGD as an industrial-scale air purifier, intercepting harmful gases before they escape into the atmosphere. The process varies based on the method used, but the two primary types are:
1. Wet Flue Gas Desulfurization Systems
Wet FGD is the most commonly used method due to its high efficiency. It involves scrubbing the flue gas with a liquid absorbent, usually a limestone (calcium carbonate) slurry. The chemical reaction between the limestone and sulfur dioxide produces calcium sulfite, which, upon further oxidation, transforms into gypsum (calcium sulfate). This byproduct can be repurposed in the construction industry for making drywall, cement, and fertilizers.
Key advantages of Wet FGD:
- High sulfur removal efficiency (up to 98%).
- Generates a marketable byproduct (gypsum).
- Effective for large-scale industrial applications.
2. Dry Flue Gas Desulfurization Systems
In dry FGD systems, a powdered lime-based sorbent is injected into the flue gas, where it reacts with SO₂ to form a dry, solid byproduct. Unlike wet systems, dry scrubbers do not produce liquid waste, making them more suitable for areas with water scarcity.
Key advantages of Dry FGD:
- Lower initial investment and operational costs.
- No wastewater treatment required.
- Suitable for medium to small-scale industries.
Both methods have their applications, and the choice between them depends on industry requirements, environmental regulations, and cost considerations.
Çözüm Yelpazemizi Keşfedin:
Why FGD is More Important Than Ever
Industrial air pollution is a growing concern, with governments worldwide enforcing stricter emissions regulations. The need for FGD technology is driven by several crucial factors:
1. Stricter Environmental Regulations
International agreements and national policies are setting aggressive targets for SO₂ reduction. For instance, the Environmental Protection Agency (EPA) in the U.S. and the Ministry of Environment, Forest and Climate Change (MoEFCC) in India have implemented stringent emission norms for power plants and industries. Non-compliance can result in heavy fines and even shutdowns.
2. Health and Environmental Impact
High SO₂ levels contribute to respiratory problems such as asthma, bronchitis, and lung infections. Additionally, sulfur dioxide reacts with other compounds in the air to form sulfate particles, which further contribute to fine particulate matter (PM2.5) pollution—a major cause of premature deaths worldwide.
From an environmental perspective, SO₂ emissions lead to acid rain, which damages crops, forests, soil, and aquatic ecosystems. By implementing FGD systems, industries can significantly reduce these harmful effects.
3. Economic Benefits and Byproduct Utilization
Contrary to the perception that pollution control technologies add to operational costs, FGD systems can be economically beneficial. The gypsum produced from wet FGD can be sold to the construction industry, providing an additional revenue stream. Similarly, the dry byproducts can be used in cement production and land reclamation projects.
Challenges and Innovations in FGD Technology
While FGD is a proven and widely adopted technology, it does come with challenges. These include high installation and maintenance costs, energy consumption, and disposal of waste byproducts. However, recent advancements are addressing these concerns.
1. Advanced Scrubbing Techniques
Modern wet scrubbers are designed to optimize limestone utilization, reduce energy consumption, and enhance SO₂ removal efficiency. Some systems even integrate dual-alkali technology, which improves performance while minimizing sludge formation.
2. AI-Driven Monitoring Systems
Artificial Intelligence (AI) and Internet of Things (IoT) solutions are transforming the efficiency of FGD systems. Smart sensors and automated controls can monitor real-time emissions, adjust reagent dosage, and optimize performance, leading to lower operational costs.
3. Alternative Sorbents and Carbon Capture Integration
Research is ongoing to explore alternative sorbents such as magnesium-based compounds, which promise higher reactivity and better SO₂ absorption. Additionally, some industries are integrating carbon capture technology with FGD systems to further reduce greenhouse gas emissions.
The Global Adoption of FGD Systems
The demand for FGD technology is surging across different industrial sectors worldwide. Here are some key industry applications:
- Enerji Santralleri: Thermal power stations are among the largest contributors to SO₂ emissions, making FGD essential for coal-fired plants.
- Cement and Steel Industry: High-temperature processes in cement kilns and steel manufacturing release significant sulfur dioxide levels, necessitating emission control.
- Petrochemical and Refining: Oil refineries process sulfur-rich crude oil, making them major SO₂ emitters. Many refineries are now investing in advanced FGD systems.
China, India, the U.S., and European countries are leading the adoption of FGD, driven by regulatory pressure and environmental commitments.
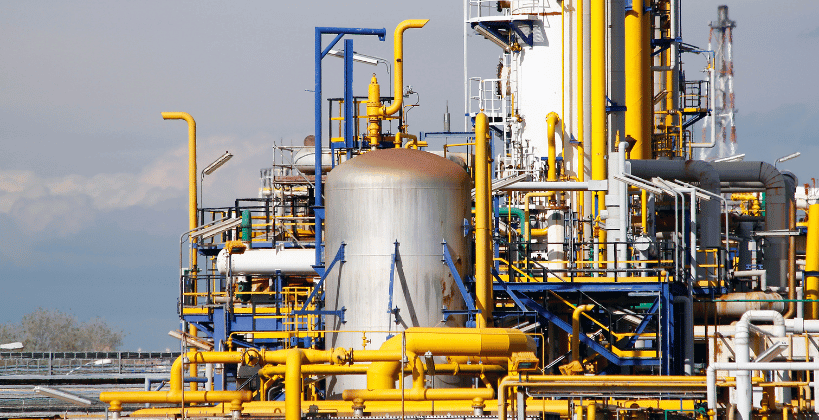
The Road Ahead: Sustainable Emission Control
As the world moves towards net-zero emissions, FGD technology will continue to evolve. The focus will be on making desulfurization processes more cost-effective, energy-efficient, and environmentally friendly.
Future developments may include:
- Hybrid FGD systems combining wet and dry techniques for enhanced efficiency.
- Integration with renewable energy sources to reduce the carbon footprint of industrial operations.
- Advanced materials and catalysts for improved SO₂ absorption and minimal waste generation.
For industries looking to stay ahead of environmental regulations and contribute to a cleaner future, investing in next-generation FGD solutions isn’t just an option—it’s a necessity.
Final Thought
Flue Gas Desulfurization is more than just a pollution control measure; it is an essential step toward sustainable industrial operations. With regulatory frameworks becoming more stringent and the global push for cleaner air intensifying, industries must adopt advanced FGD technologies to remain compliant and environmentally responsible.
Are you exploring Flue Gas Desulfurization solutions for your industry? Reach out to our experts today to find a customized system that meets your operational needs and sustainability goals.