Cyclone separators are crucial for industrial operations requiring efficient dust and particulate removal from gas streams. These devices are widely recognized for their ability to enhance air quality, reduce emissions, and support environmental sustainability. Built with a simple yet effective design, Separators rely on centrifugal force to separate dust particles, making them durable, low-maintenance, and cost-effective. They are an integral part of various industries, ensuring clean air for employees, compliance with regulatory standards, and efficient operation of industrial processes.
Working Principles of Cyclone Separators
Cyclone separators operate by inducing a rotational motion in the dust-laden gas stream. The air enters the separator tangentially, creating a spiral motion. Heavier particles, due to centrifugal force, are flung toward the walls of the separator, where they lose momentum and drop into a collection chamber. The cleaned air then exits through the central outlet at the top. This simple mechanism requires no moving parts, filters, or additional consumables, making Separators a reliable and long-lasting solution for industries handling particulate matter.
Understanding Cyclone Separators
Cyclone separators are mechanical devices that use centrifugal forces to remove dust and particulates from gas streams. Unlike filters, they operate without moving parts or consumables, making them durable and low-maintenance solutions for air pollution control
How Cyclone Separators Work:
- Air Inlet: Dust-laden gas enters the cyclone tangentially, creating a spiral motion.
- Centrifugal Force: As the gas rotates, heavier particles are pushed outward toward the cyclone walls.
- Dust Collection: The particles lose momentum and drop into the collection chamber at the bottom.
- Clean Air Exit: The cleaned gas stream exits through a central outlet at the top of the cyclone.
Benefits of Using Cyclone Separators
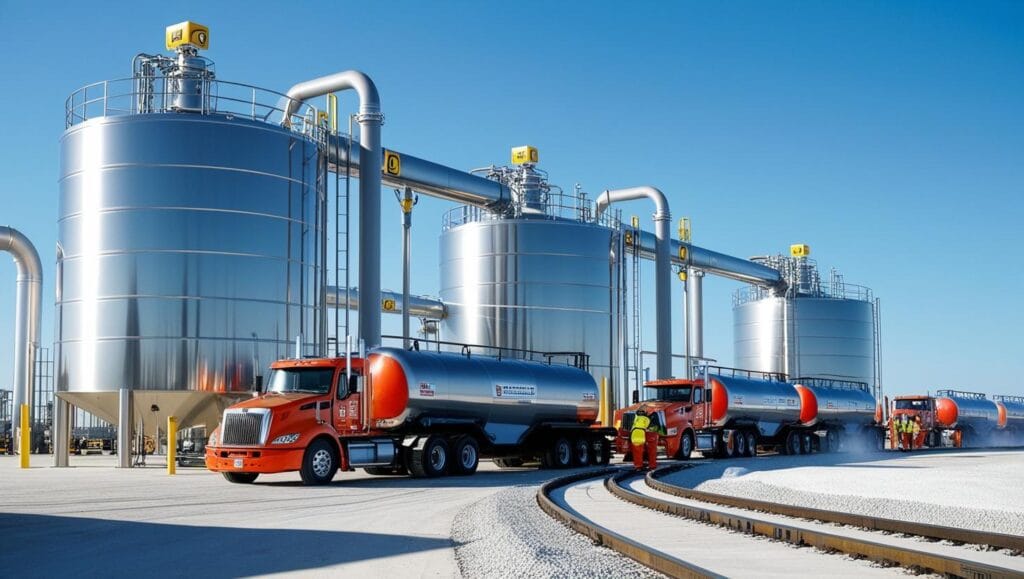
Cyclone separators offer numerous advantages that make them indispensable in industrial air pollution control systems. One of their most significant benefits is their ability to efficiently capture a wide range of particle sizes, ensuring clean exhaust air. Their design eliminates the need for frequent maintenance, as there are no filters or moving parts to replace. This reduces operational downtime and lowers maintenance costs. Constructed from durable materials, Separators can withstand harsh conditions, including abrasive particles and high temperatures. They also consume minimal energy during operation, making them a cost-effective solution for industries focused on optimizing operational expenses.
Another noteworthy feature is their versatility. Separators can handle different types of particles and gas streams, making them suitable for industries ranging from power generation to food processing. By incorporating modern innovations, separators are increasingly becoming more energy-efficient, ensuring industries meet sustainability goals while maintaining high operational standards.
당사의 솔루션 범위를 알아보세요:
Applications of Cyclone Separators Across Industries
Cyclone separators are used extensively in various industries to address particulate matter challenges. In cement manufacturing, they are deployed to capture fine cement dust from kilns and grinding mills, thereby reducing emissions and improving workplace safety. Power plants rely on separators to remove fly ash from flue gases, which is essential for meeting stringent environmental regulations. Metal production facilities benefit from cyclone separators by capturing metallic dust and fumes during processes like smelting and refining, ensuring cleaner air and protecting sensitive equipment.
In wood processing, cyclone separators are used to remove sawdust and wood particles from exhaust air, reducing fire hazards and improving air quality for workers. Food processing industries also depend on cyclone separators to ensure product purity by separating dust and fine particles from air streams during milling and packaging operations. In the chemical industry, cyclone separators handle fine powders and corrosive gases, safeguarding both product quality and equipment longevity.
Enhancing Cyclone Separator Efficiency
While cyclone separators are inherently efficient, certain improvements can further enhance their performance. Optimizing the geometry of the cyclone, such as adjusting the diameter, height, and inlet design, can significantly reduce turbulence and improve separation efficiency. The use of wear-resistant materials ensures that the separator can handle abrasive particles without frequent wear and tear. Incorporating advanced materials also allows separators to perform efficiently in high-temperature environments.
Integrating heat recovery systems into cyclone designs is another way to boost efficiency. By capturing and reusing heat from industrial processes, these systems not only enhance energy efficiency but also contribute to cost savings. Additionally, advanced monitoring technologies, such as IoT-enabled sensors, can track performance metrics in real time, enabling predictive maintenance and reducing unexpected downtime.
The Role of Cyclone Separators in Environmental Sustainability
Cyclone separators play a vital role in promoting environmental sustainability by minimizing particulate emissions from industrial processes. They help industries meet stringent air quality standards, ensuring compliance with environmental regulations. Furthermore, the energy-efficient operation of modern cyclone separators reduces the carbon footprint of industrial facilities. By preventing particulate pollution, these devices protect ecosystems and contribute to cleaner and healthier surroundings.
Another critical aspect of separators is their ability to handle byproducts effectively. Many industries generate valuable materials, such as fly ash in power plants, that can be recycled and repurposed. separators help collect these materials efficiently, reducing waste and supporting circular economy initiatives.
지금 우리와 연결하세요
Innovations in Cyclone Separator Technology
As industries evolve, so do cyclone separators. The integration of advanced technologies has transformed their performance and applications. Smart separators equipped with IoT sensors allow real-time monitoring, helping industries optimize efficiency and plan maintenance schedules proactively. Hybrid systems that combine separators with other dust collection technologies, such as bag filters or electrostatic precipitators, enhance the capture of fine particles, ensuring comprehensive dust separation.
Modern cyclone designs are also focusing on sustainability. By using recyclable materials and energy-efficient components, manufacturers are reducing the environmental impact of these devices. Compact designs are becoming increasingly popular, allowing industries to integrate cyclone separators into processes with limited space. These advancements ensure that cyclone separators remain a vital tool for industrial dust control while aligning with sustainability goals.
결론
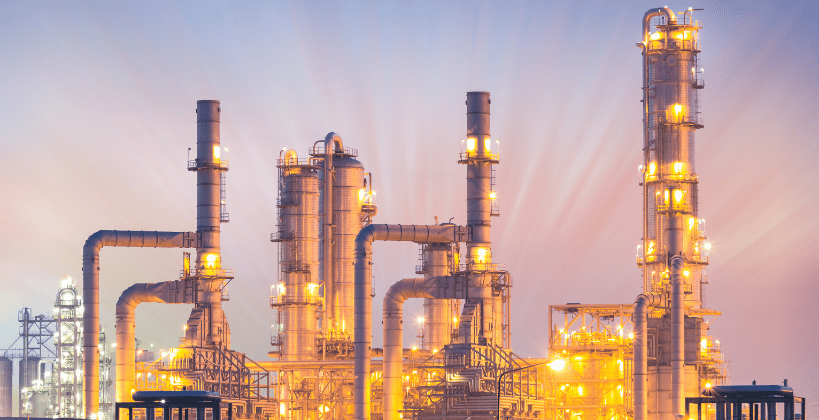
Cyclone separators are indispensable for industries seeking efficient and reliable solutions for dust and particulate separation. Their robust design, low maintenance requirements, and adaptability to various applications make them a preferred choice for industries ranging from cement production to food processing. As environmental regulations become stricter and the demand for sustainable operations grows, separators continue to evolve with innovative technologies that enhance their performance and efficiency.
By investing in modern cyclone separators, industries can achieve cleaner operations, reduce emissions, and contribute to a healthier and more sustainable future. Whether optimizing existing processes or designing new ones, separators offer a proven and effective solution for industrial air pollution control.