The cement industry plays a vital role in global infrastructure development. However, the production process generates significant amounts of dust, posing both health and safety hazards. In recent years, ATEX (ATmosphères EXplosibles) compliance has become increasingly important for dust collection systems in cement plants.
The colossal structures that define our modern world – bridges, skyscrapers, dams – all owe their existence to a seemingly mundane material: cement. This ubiquitous building block underpins global infrastructure development, from bustling megacities to remote rural communities. The cement production process, however, is not without its challenges. One significant concern lies in the generation of large quantities of dust.
While the primary components of cement dust – limestone, clay, and other minerals – are not inherently toxic, their sheer volume can pose health hazards and visibility issues for workers. However, a more serious threat lurks beneath this seemingly innocuous dust cloud: its explosive potential. When suspended in air at specific concentrations, cement dust can readily ignite with a spark, creating a devastating explosion.
Historically, these explosions have caused tragic accidents in cement factories worldwide. The jarring reality of these incidents has led to a growing awareness of the dangers posed by combustible dusts. This, coupled with a heightened commitment to worker safety, has fueled the rise of ATEX (ATmosphères EXplosibles) compliance in dust collection systems within the cement industry.
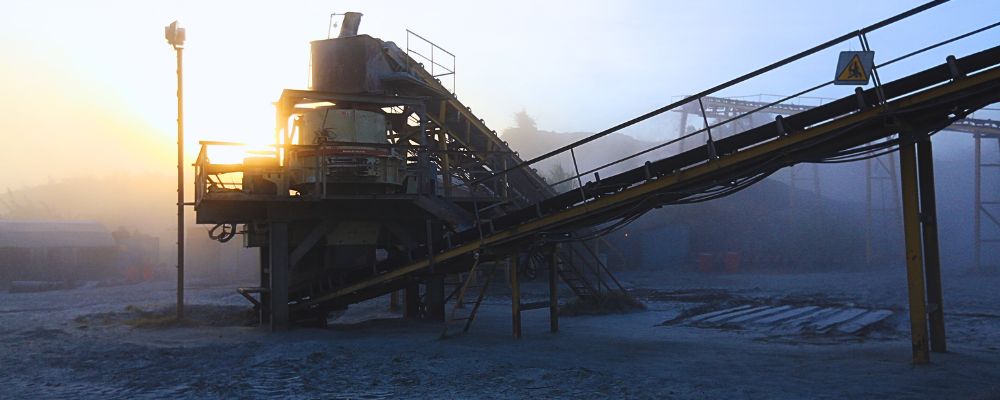
Why is ATEX Compliance Rising in Importance in Cement Industry?
The growing prominence of ATEX compliance in dust collection systems for cement manufacturers isn’t merely a regulatory formality; it represents a multifaceted approach to safety within the industry.
Here, we dissect the key factors driving this rise:
- Heightened Awareness of Explosion Risks: The devastating consequences of historical dust explosions in cement plants have served as a stark reminder of the explosive potential of seemingly innocuous materials. This newfound awareness has spurred a collective effort to prioritize worker safety and prevent such tragedies from repeating.
- Commitment to Worker Wellbeing: Modern work environments strive to prioritize the health and safety of employees. ATEX compliance embodies this commitment by mandating stricter safety measures in areas with a high risk of dust explosions. This not only protects workers from immediate physical harm but also fosters a culture of safety awareness within the workplace.
- Evolving Regulatory Landscape: Regulatory bodies around the world are continuously revising and strengthening regulations pertaining to dust control and explosion prevention. ATEX compliance reflects this evolving landscape, ensuring cement manufacturers adhere to the latest safety standards and best practices.
- Improved Risk Mitigation Strategies: The ATEX directives provide a comprehensive framework for assessing and mitigating explosion risks. By implementing these strategies, cement manufacturers can proactively identify potential hazards and implement safeguards to minimize the likelihood of explosions.
- Enhanced Insurance Coverage: Many insurance companies are increasingly recognizing the value of ATEX compliance. Facilities demonstrating adherence to these regulations may be eligible for more favorable insurance terms, reflecting the lower risk profile associated with a well-managed dust collection system.
By acknowledging these factors, manufacturers can readily understand why ATEX compliance is no longer simply a regulatory requirement but a crucial pillar of a safety-conscious and future-proof cement production operation.
ATEX Compliance in Dust Collection: Roadmap for Cement Manufacturers
For cement manufacturers, achieving optimal dust collection within their facilities goes beyond just maintaining air quality. The rise of ATEX (ATmosphères EXplosibles) compliance has introduced a new layer of importance, transforming dust collection systems into critical safety components. This section serves as a roadmap, guiding cement manufacturers through the key steps involved in achieving ATEX compliance:
- Comprehensive Risk Assessment: The journey begins with a meticulous risk assessment. This in-depth analysis identifies and classifies areas within the facility where explosive dust atmospheres might occur. Factors like dust concentration, particle size distribution, and potential ignition sources are meticulously evaluated to create a clear picture of the existing risk profile.
- Zoning the Facility: Based on the findings of the risk assessment, the facility is then divided into distinct zones. These zones are designated with varying levels of explosion risk, with stricter safety measures mandatory in higher-risk areas. This zoning approach allows for targeted mitigation strategies, optimizing resource allocation and ensuring maximum safety where it’s needed most.
- Selecting the Right Equipment: Not all dust collection equipment is created equal, especially when it comes to ATEX compliance. Cement manufacturers require systems specifically designed and certified for safe operation in explosive atmospheres. This includes features like explosion venting channels to safely release pressure, robust construction materials to prevent ignition through sparks, and integrated flame suppression systems to extinguish flames within the dust collector itself.
- Maintaining a Culture of Safety: ATEX compliance isn’t a one-time achievement but rather an ongoing process. Cement manufacturers must foster a culture of safety awareness within their workforce. This includes providing employees with proper training on ATEX regulations, safe dust collection practices, and emergency procedures in case of an incident.
Intensiv-Filter Himenviro: Your Trusted Partner in ATEX-Compliant Dust Collection for Cement Manufacturers
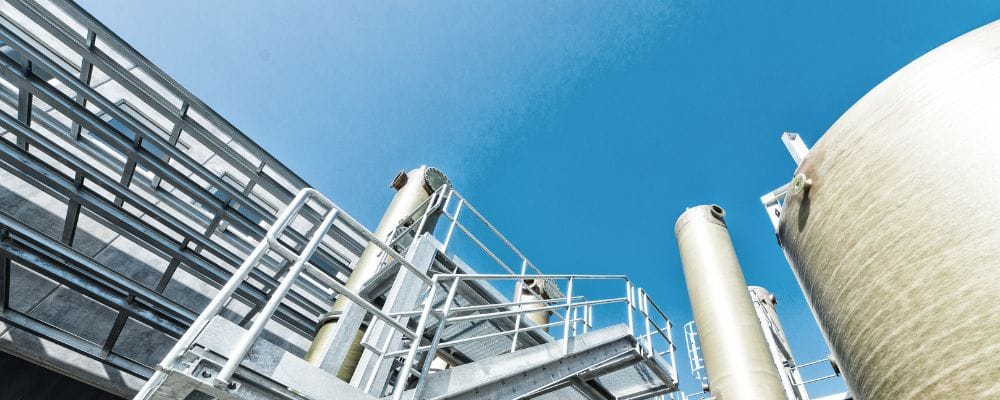
In the ever-evolving landscape of cement production, navigating the complexities of ATEX compliance can feel like a daunting task. Intensiv-Filter Himenviro emerges as your steadfast partner on this journey, offering a comprehensive range of ATEX-certified dust collection systems specifically designed for the unique challenges of cement plants. We go beyond mere equipment providers, transforming ourselves into a collaborative force for safety and efficiency within your operation. Here’s why Intensiv-Filter Himenviro stands out:
- Unwavering Commitment to ATEX Expertise: Our team possesses in-depth knowledge of ATEX regulations and their application within the cement industry. We leverage this expertise to guide you through the entire process, from initial risk assessment and zoning to equipment selection and installation.
- ATEX-Certified Solutions Tailored for Cement Dust: We understand that cement dust presents unique challenges. Our dust collection systems are not only ATEX-certified but also specifically engineered to handle the demanding environment and explosive potential of cement dust particles.
- Rugged Construction Built to Last: Cement production facilities are tough environments. Our systems are built with robust materials and meticulous attention to detail, ensuring they can withstand the rigors of continuous operation and harsh conditions.
- Focus on Optimal Efficiency: While safety remains paramount, we also recognize the importance of efficiency. Our ATEX-compliant systems are designed to optimize dust collection performance, minimizing downtime and maximizing production output for your cement plant.
- Unwavering Dedication to Customer Service: We understand that your needs are unique. Our dedicated team provides personalized customer service, working closely with you to understand your specific requirements and tailor a solution that perfectly integrates into your existing infrastructure.
By choosing Intensiv-Filter Himenviro, you gain more than just ATEX-compliant dust collection equipment; you gain a trusted partner committed to your safety and operational success. Let us guide you on the path to a safer and more efficient future for your cement production facility.