Industries that emit particulate matter face strict environmental regulations, compelling them to adopt advanced filtration systems that not only capture fine particles but also remain durable, energy-efficient, and cost-effective. Reverse air bag houses have long been a reliable solution in applications where large volumes of gas require filtration. Now, with the integration of nanofiber technology into filter media, the capabilities of these systems are being significantly enhanced. Nanofiber media introduces unique qualities, allowing reverse air bag houses to capture ultra-fine particles, improve mechanical resilience, and reduce energy usage—key benefits in industrial settings.
This article delves into the role of nanofiber-enhanced media for reverse air bag houses, examining how it improves efficiency, durability, and operational costs. Additionally, we explore how Intensiv-Filter Himenviro leverages this technology to provide high-performance filtration solutions that meet the needs of various industries.
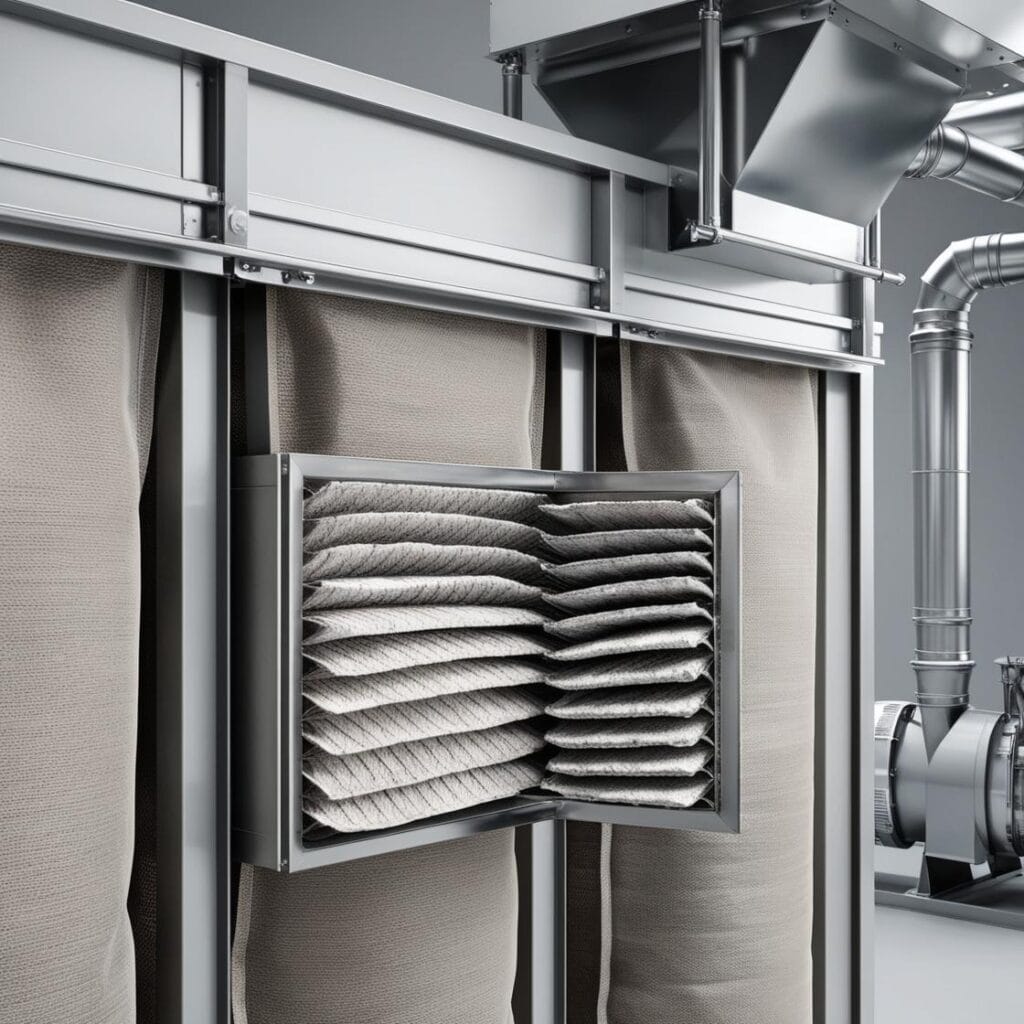
What Are Reverse Air Bag Houses?
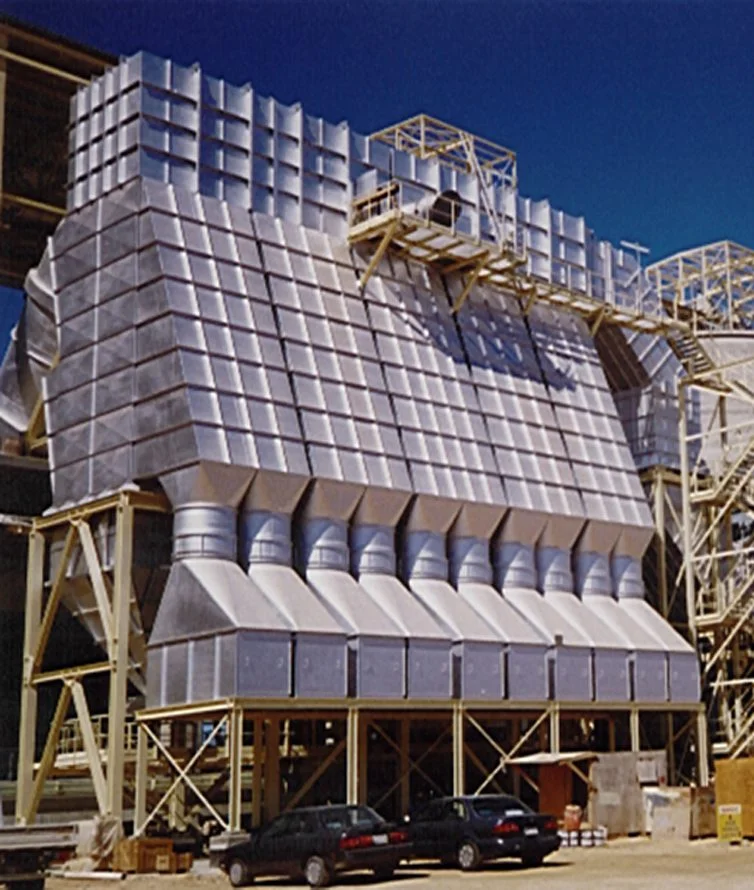
Reverse air bag houses are large dust collection systems that operate by pulling air laden with dust or particulates through a set of filter bags. Unlike pulse-jet bag houses, which rely on bursts of compressed air for cleaning, reverse air systems employ a gentle reverse flow of air to dislodge particles from the filter surface. This method is less abrasive, extending the life of the filter media. Industries such as cement production, mining, and metal processing commonly use reverse air bag houses to control emissions and ensure compliance with environmental standards.
Challenges in Traditional Filter Media
Despite their effectiveness, traditional filter media in reverse air bag houses face several challenges:
- Limited Efficiency in Capturing Ultra-Fine Particles: Standard materials may struggle with submicron particles, which can easily bypass the fibers, reducing overall filtration efficiency.
- Mechanical Wear and Tear: The continuous flow of particulates can weaken traditional fibers, leading to frequent replacements and higher maintenance costs.
- Energy Consumption: The air flow required to operate a reverse air bag house adds to the energy footprint, an important consideration in industrial applications where efficiency is paramount.
Nanofiber technology addresses these challenges by enhancing filtration media to handle finer particles, reduce operational energy, and extend the life of the filter bags, making it an ideal advancement for reverse air systems.
Discover Our Range of Solutions:
The Advantages of Nanofiber-Enhanced Filter Media
1. Improved Filtration Efficiency for Ultra-Fine Particles
Nanofibers have diameters as small as 100 nanometers, creating an ultra-fine network that captures particles down to the submicron level. By layering nanofibers onto traditional media, nanofiber-enhanced filters provide a greater surface area and a tighter mesh, effectively capturing finer particles that would otherwise escape. This makes them particularly suitable for applications with stringent emissions standards and industries dealing with fine dust or smoke, such as cement manufacturing and steel production.
2. Enhanced Mechanical Durability
Traditional filter materials, while effective in the short term, often deteriorate under constant exposure to high dust loads, leading to frequent replacements. Nanofiber coatings help extend the life of these filters by reinforcing the media, adding an extra layer that reduces fiber degradation and mechanical wear. This durability is especially beneficial for reverse air systems, where the continuous reverse airflow can cause gradual weakening of conventional filter media.
3. Reduced Pressure Drop and Energy Consumption
Nanofiber media’s design minimizes resistance to airflow, resulting in a lower pressure drop across the filter. This allows reverse air bag houses to operate more efficiently, reducing the energy required to maintain airflow and lowering operational costs. The reduced energy consumption not only benefits the company’s bottom line but also contributes to environmental sustainability by decreasing the facility’s energy footprint.
4. Longer Service Life and Lower Maintenance Costs
The enhanced durability of nanofiber filter media translates to longer service intervals and lower maintenance requirements. This extended lifespan reduces downtime and the frequency of replacements, making it a cost-effective choice for high-demand applications. Nanofiber filters can withstand multiple cleaning cycles without significant degradation, which is particularly valuable in industries where maintenance interruptions can lead to substantial losses.
Connect with us Now
Applications of Nanofiber Media in High-Demand Industries
Cement Industry
In cement production, dust control is critical as processes generate a high volume of particulates. Nanofiber media offers a solution that captures ultra-fine cement dust, significantly improving air quality. Additionally, the enhanced durability of nanofiber filters supports the continuous operation required in cement kilns, reducing downtime and maintenance.dapibus leo.
Mining and Quarrying
Mining operations produce large amounts of dust that contain various particle sizes. Standard filters may struggle to capture the smaller particulates. Nanofiber-enhanced media enables reverse air bag houses to effectively filter out fine dust and mineral particles, even in harsh environmental conditions, providing a cleaner and safer work environment.
Metal Processing
The metal industry produces fine particulates from processes like grinding, melting, and refining. Nanofiber filter media ensures high-efficiency capture of metallic and toxic particles, addressing environmental standards and protecting workers from airborne contaminants. In metal processing, where durability is essential, nanofiber media extends the operational lifespan of filtration systems, supporting longer production cycles.
Power Generation
Power plants often rely on reverse air bag houses for controlling fly ash and particulate emissions. Nanofiber filters not only capture finer particles but also reduce energy consumption, supporting power plants’ efforts to maintain cost-effective and environmentally compliant operations. With energy efficiency being a priority, nanofiber filters provide an optimal solution for power plants seeking to reduce emissions and operational costs.
Innovations in Nanofiber Technology for Reverse Air Bag Houses
Advanced Coating Techniques
New coating methods allow for the even distribution of nanofibers across filter media, ensuring consistent filtration efficiency and durability. By integrating nanofibers into multi-layer filter materials, manufacturers can produce media that combines the strengths of multiple fibers for optimal performance.
Self-Cleaning Capabilities
Some modern nanofiber filters are equipped with self-cleaning capabilities that reduce the frequency of maintenance. These filters can resist clogging by allowing particulate matter to dislodge more easily during the reverse air cleaning cycle, enhancing system reliability and reducing downtime.
Customizable Designs for Specific Applications
Nanofiber media can be tailored for specific industrial applications, including high-dust and high-heat environments. Customizable designs make these filters versatile, meeting the exact needs of industries from cement to power generation, where application-specific requirements are essential for efficient operation.
How Intensiv-Filter Himenviro Supports High-Performance Nanofiber Filtration



Intensiv-Filter Himenviro has been at the forefront of air filtration technology, providing innovative solutions tailored for high-demand industrial applications. The integration of nanofiber media into reverse air bag houses is one of their key advancements, addressing the unique challenges faced by industries with high dust loads and stringent emission standards.
Expertise in Nanofiber Media Integration
Intensiv-Filter Himenviro offers advanced nanofiber media that enhances the efficiency and durability of reverse air bag houses. Their filters capture ultra-fine particles, providing compliance with even the most rigorous environmental regulations. By integrating these advanced materials, Intensiv-Filter Himenviro helps clients achieve higher filtration efficiency while reducing maintenance costs.
Custom Solutions for Industry-Specific Challenges
Understanding that each industry has unique requirements, Intensiv-Filter Himenviro provides customizable nanofiber filters tailored to specific applications. Whether in cement kilns, mining sites, or power plants, their nanofiber-enhanced filters are designed to withstand challenging environments, providing reliable and long-lasting performance.
Focus on Energy Efficiency and Sustainability
Intensiv-Filter Himenviro’s commitment to sustainability is reflected in their energy-efficient designs. Nanofiber media in reverse air systems reduces energy consumption, aligning with industries’ efforts to decrease their environmental impact. This focus on sustainability not only supports cleaner air but also allows clients to reduce operational costs.
Comprehensive Support and Expertise
From system design to installation and maintenance, Intensiv-Filter Himenviro provides end-to-end support to ensure the optimal performance of filtration systems. Their team of experts collaborates with clients to implement the best filtration solutions, adapting nanofiber technology to meet the specific demands of each industrial application.
Future Prospects for Nanofiber Filtration in Reverse Air Bag Houses
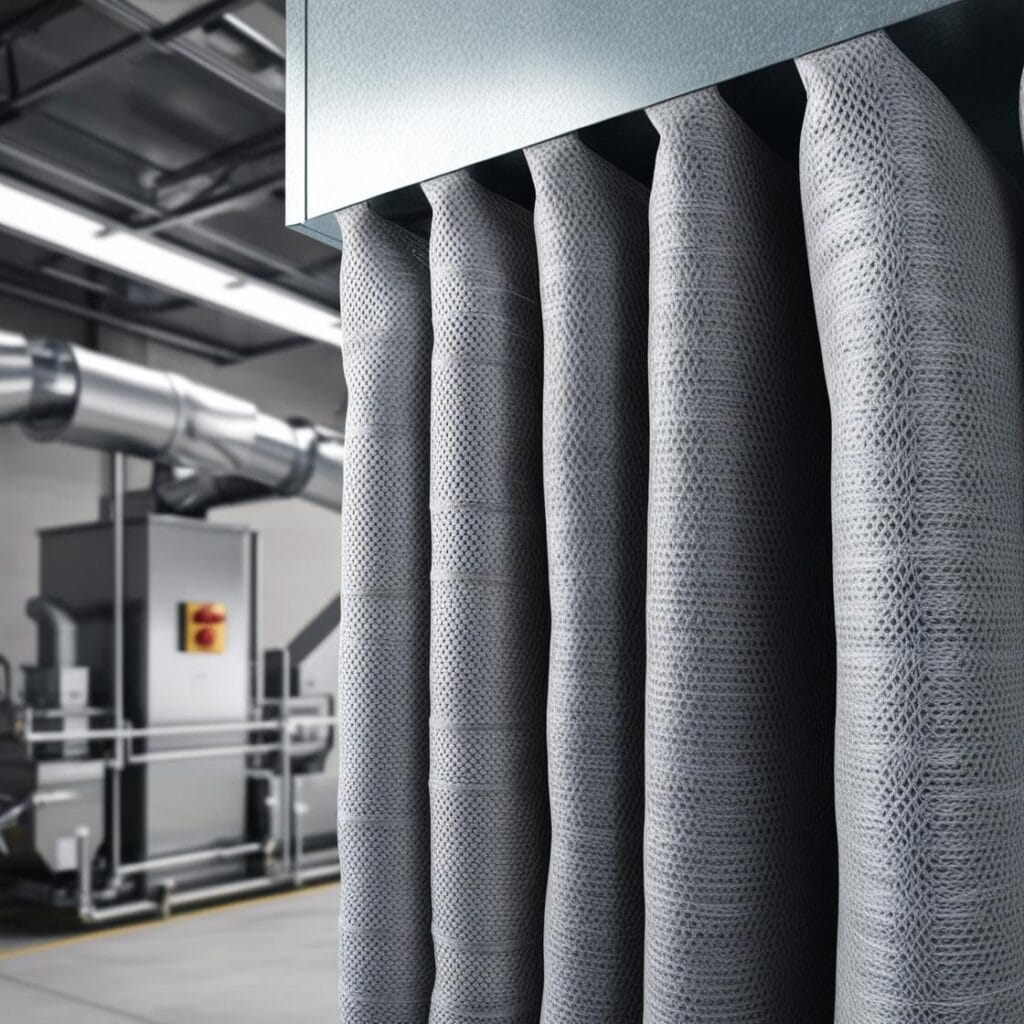
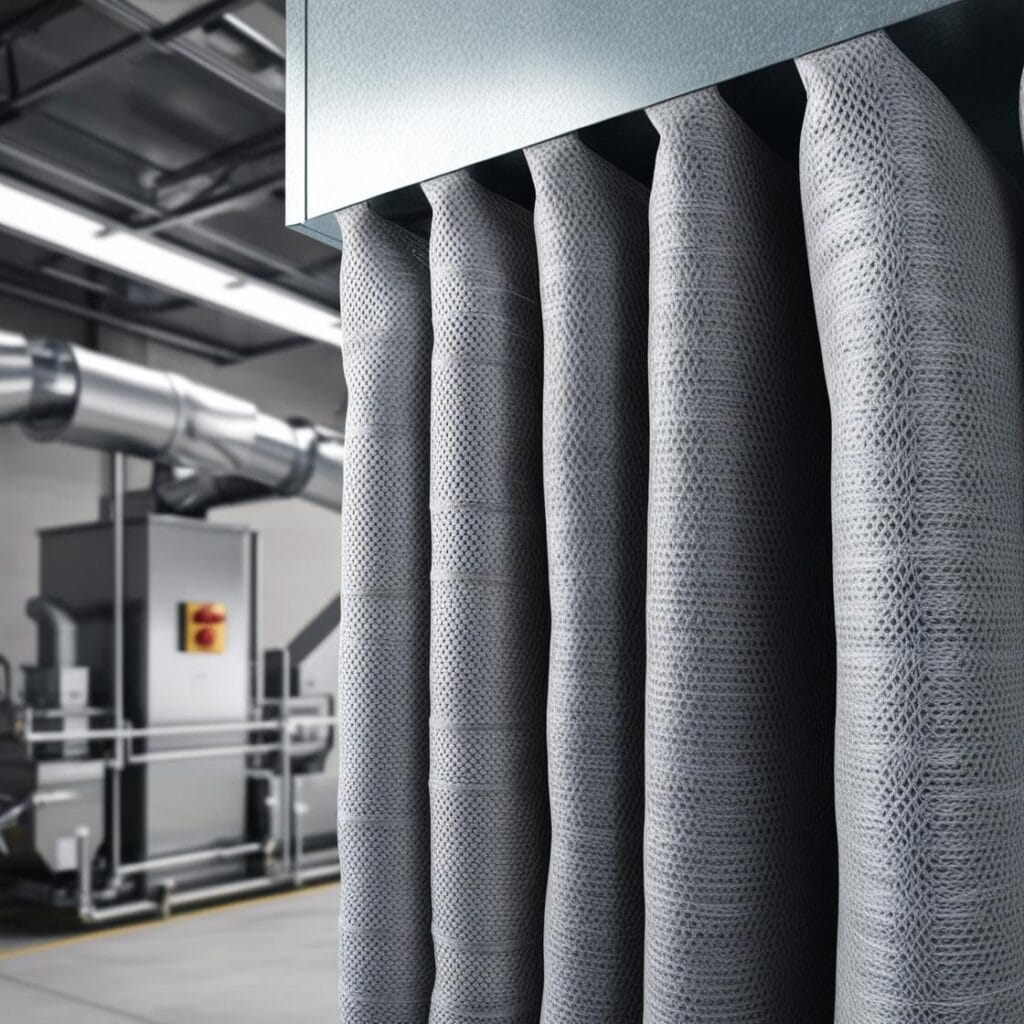
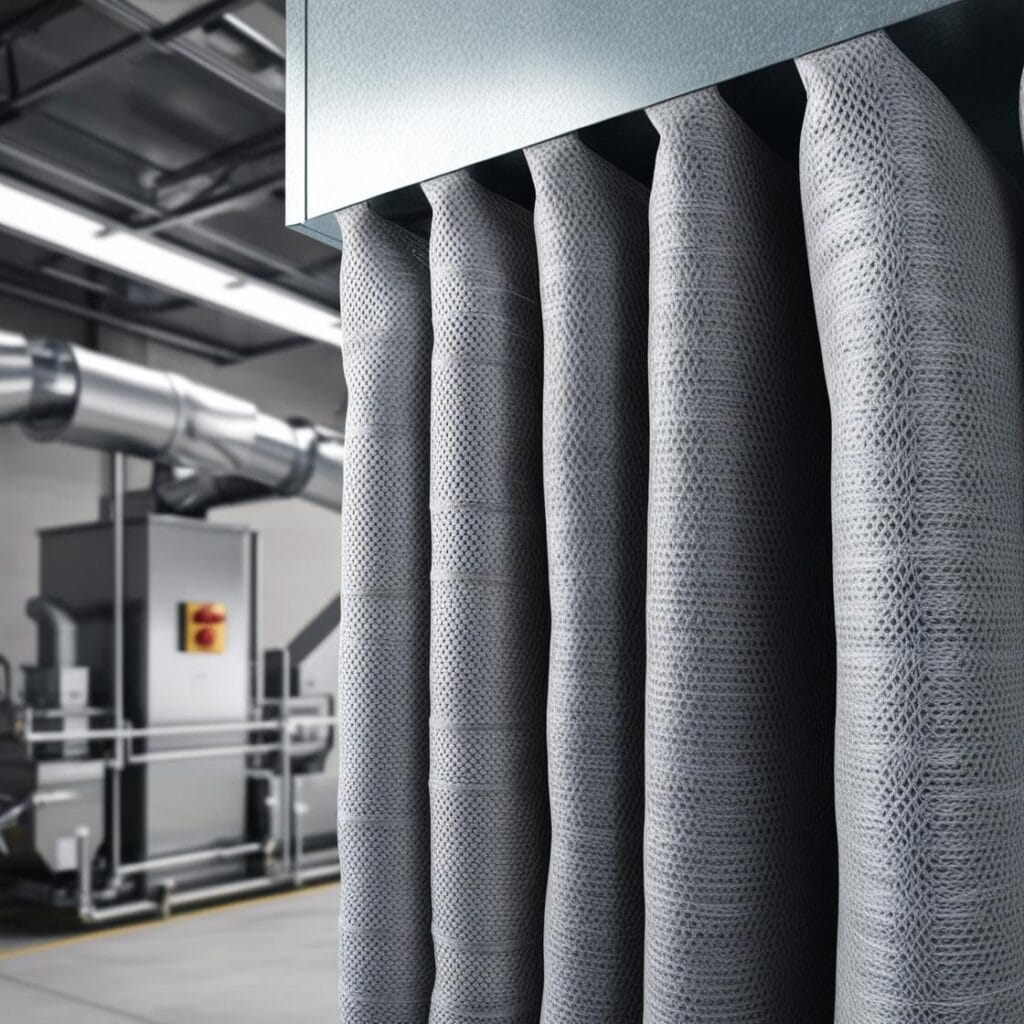
The evolution of nanofiber technology continues to drive innovations in industrial filtration. As environmental regulations tighten and industries prioritize operational efficiency, nanofiber-enhanced filters are likely to become a standard in high-demand filtration applications. With further advancements in materials science, these filters will become even more effective and adaptable, providing industries with the tools to meet their filtration needs sustainably.
Intensiv-Filter Himenviro remains dedicated to advancing filtration technology, pioneering nanofiber media that offers cleaner air, extended durability, and reduced energy consumption. As industrial applications evolve, Intensiv-Filter Himenviro’s solutions will continue to support industries in achieving compliance, operational efficiency, and environmental sustainability.