In industries that emit particulate-laden exhaust gasses, air pollution control systems are critical. From cement plants and power generation facilities to chemical processing units, managing both fine and coarse particles in emission streams is an ongoing challenge. Over the years, various filtration technologies have evolved to meet increasingly stringent environmental regulations and operational demands. Among these, Electrostatic Precipitators (ESPs) and mechanical filters (such as baghouses and fabric filters) have been the most commonly used systems.
However, with the ever-growing need for more efficient air pollution control solutions, hybrid filtration technologies that combine the benefits of ESPs and mechanical filters have emerged as a promising alternative. This hybrid approach optimizes particle removal by targeting both fine and coarse particulates, leading to enhanced air quality and more efficient pollution control.
This article delves into the structure, mechanism, and benefits of hybrid filtration technologies, exploring their applications across various industries and their potential to become the new standard for air quality control.
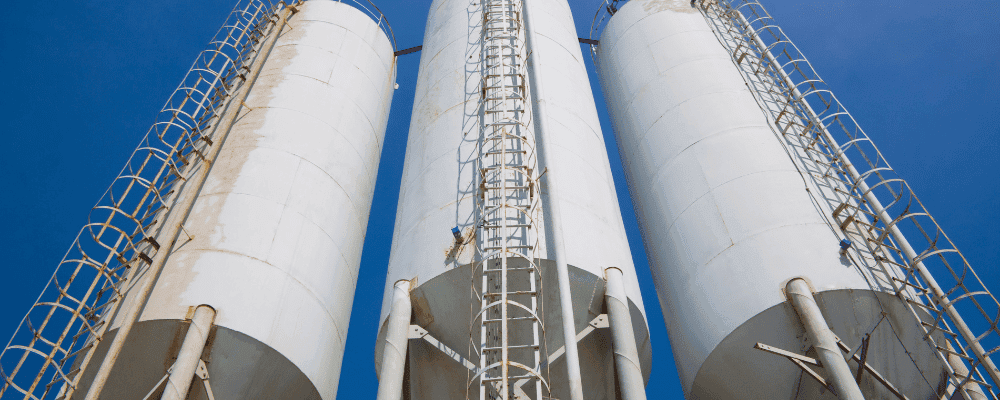
Tuklasin ang Aming Saklaw ng Mga Solusyon:
Understanding Electrostatic Precipitators (ESPs)
Electrostatic Precipitators (ESPs) have been used for decades as an effective method for removing fine particles from industrial gas streams. The ESP operates by electrically charging the particles in the gas flow and then capturing them on oppositely charged collector plates.
The process involves several stages:
- Ionization: Gas passes through a region where a high voltage electric field is applied. This electric field ionizes the gas molecules and charges the particles.
- Collection: The charged particles move toward collector plates with an opposite charge, adhering to them as the gas passes through.
- Dust Removal: Periodically, the collector plates are cleaned through mechanical rapping, dislodging the collected particles into a hopper below.
While ESPs are highly effective at capturing fine particles (those smaller than 10 microns), they can struggle with larger, coarse particulates. In addition, their performance can be affected by factors such as particle resistivity, gas temperature, and humidity, potentially reducing efficiency under certain operating conditions.
Mechanical Filtration: The Role of Fabric Filters and Baghouses
Mechanical filters, particularly baghouses, are another key technology used for dust collection in industrial environments. Unlike ESPs, which use electrostatic forces, baghouses and fabric filters rely on physical filtration to capture particles from gas streams.
A typical baghouse consists of multiple filter bags made from various materials such as woven or felted fabrics. These bags allow gas to pass through while capturing particulate matter on the surface or within the filter media.
The working principle of a baghouse is simple:
- Filtration: The gas passes through the filter bags, where particles are trapped.
- Cleaning: Once a sufficient amount of dust accumulates, the filter bags are cleaned using methods like reverse air, shaker mechanisms, or pulse-jet cleaning, dislodging the particles into a collection hopper.
Mechanical filters are highly effective at removing both fine and coarse particles, making them versatile for a wide range of industrial applications. However, they can face challenges in handling high-temperature gas streams and are prone to clogging if not properly maintained. Moreover, the high-pressure drop across the filter media can lead to increased energy consumption.
The Rise of Hybrid Filtration Technologies
With the limitations of standalone ESPs and mechanical filters in mind, hybrid filtration technologies have emerged as a solution to optimize the removal of both fine and coarse particulates. These hybrid systems combine the strengths of both ESPs and mechanical filters, providing a more comprehensive approach to particulate control.
In a hybrid filtration system, the ESP stage is typically placed before the mechanical filter. This allows the ESP to remove fine particles from the gas stream first, reducing the particle load on the downstream mechanical filter. The mechanical filter then captures the remaining coarse particles and any fine particles that may have escaped the ESP.
This dual-stage process offers several key benefits:
- Enhanced Efficiency: By combining two different filtration mechanisms, hybrid systems can achieve higher particulate removal efficiencies, particularly in handling a wide range of particle sizes.
Reduced Maintenance and - Operational Costs: The ESP removes a significant portion of the particulate load before it reaches the mechanical filter, reducing the frequency of filter cleaning and extending the life of the filter media.
- Lower Energy Consumption: Because the ESP handles much of the fibne particle removal, the overall pressure drop across the hybrid system can be lower compared to a standalone baghouse, reducing the energy required for operation.
- Adaptability to Different Operating Conditions: Hybrid systems can be tailored to perform efficiently across a wide range of temperatures, particle types, and gas compositions, making them suitable for diverse industrial applications.
- Improved Air Quality: The combination of ESP and mechanical filtration technologies results in cleaner gas streams with lower levels of particulate emissions, contributing to better air quality and environmental compliance.
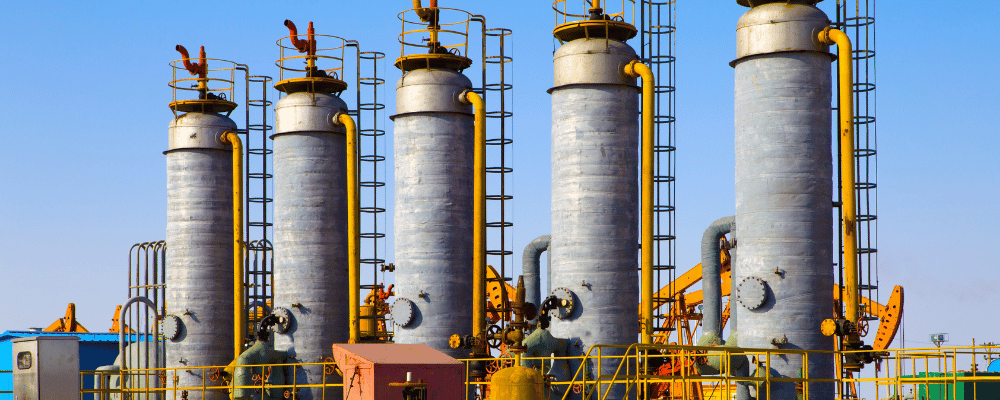
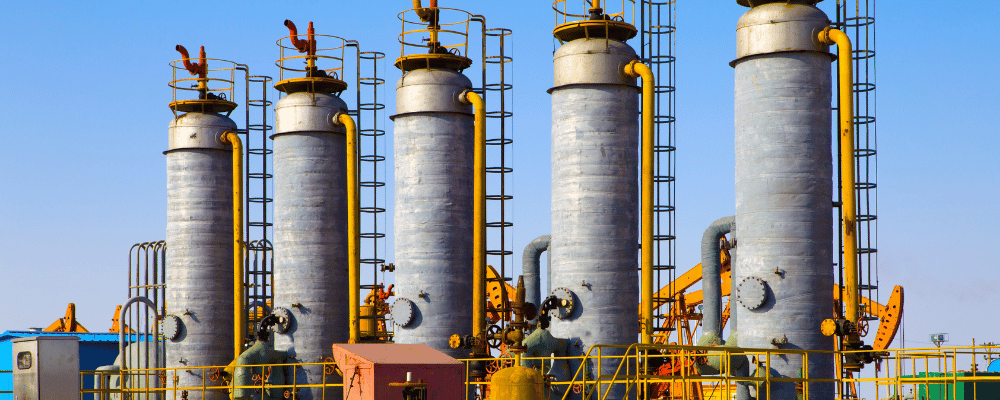
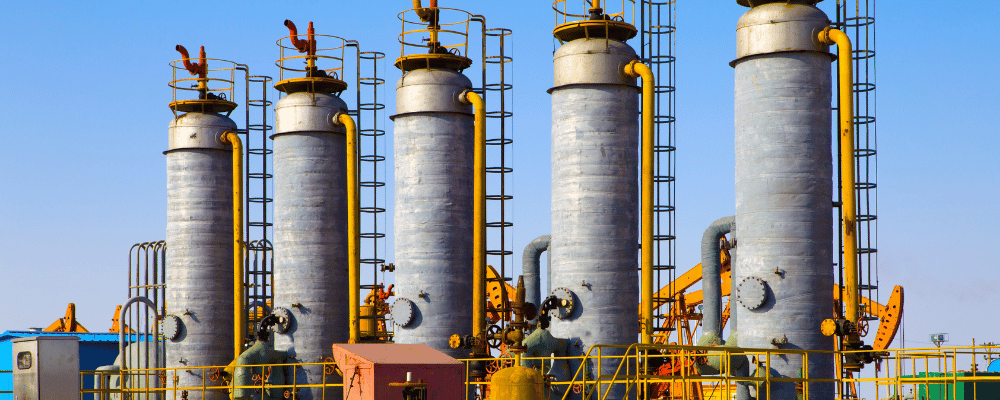
How Hybrid Filtration Works
The operation of a hybrid filtration system is a well-coordinated process, where each stage performs its specific function to optimize overall filtration efficiency. The general configuration involves the following stages:
- Pre-Electrostatic Precipitation: As the gas enters the hybrid system, it first passes through the ESP section. Here, fine particles are charged and collected on the oppositely charged collector plates, removing a large percentage of sub-micron and micron-sized particulates.
- Mechanical Filtration: After the ESP section, the gas enters the mechanical filtration section, typically a baghouse. The remaining coarse particles and any fine particles that escaped the ESP are captured by the filter media, ensuring comprehensive particle removal.
- Cleaning and Collection: As in standalone systems, both the ESP plates and filter bags are periodically cleaned to remove accumulated dust. This can be done through rapping for ESPs and reverse air or pulse-jet cleaning for the baghouse.
The integration of these two technologies allows hybrid systems to achieve particulate removal efficiencies of over 99%, even in demanding industrial environments with high particulate loads.
Key Benefits of Hybrid Filtration Systems
Optimized Particle Removal Across All Sizes
One of the key strengths of hybrid filtration systems is their ability to target a wide range of particle sizes. Fine particles, which can be challenging to capture using mechanical filtration alone, are effectively removed by the ESP section. At the same time, coarse particles, which may be difficult for ESPs to handle, are captured by the mechanical filter. This dual approach ensures that both fine and coarse particles are removed from the gas stream, resulting in cleaner emissions.
Extended Filter Life
In standalone mechanical filtration systems, the filter media can become clogged relatively quickly, particularly when handling gas streams with high particulate loads. In hybrid systems, however, much of the fine particulate matter is removed by the ESP before it reaches the mechanical filter. This reduces the overall particulate load on the filter media, extending its lifespan and reducing maintenance requirements.
Lower Energy Consumption
Mechanical filters, especially baghouses, typically create a significant pressure drop as the gas passes through the filter media. This pressure drop can result in increased energy consumption to maintain the required gas flow. In hybrid systems, the ESP removes a large percentage of the fine particles, reducing the particulate load on the mechanical filter. As a result, the pressure drop across the system is lower, leading to reduced energy consumption and operating costs.
Improved Operational Flexibility
Industrial processes can vary significantly in terms of gas composition, temperature, and particulate load. Hybrid filtration systems are highly adaptable, capable of handling a wide range of operating conditions without sacrificing efficiency. The ESP section can be fine-tuned to handle specific particle sizes or gas compositions, while the mechanical filtration section can be customized to accommodate different filter media or cleaning mechanisms.
Compliance with Stringent Emission Regulations
Many industries face increasingly stringent emission regulations, particularly in terms of particulate emissions. Hybrid filtration systems are capable of achieving particulate removal efficiencies of over 99%, making them a reliable choice for industries looking to meet or exceed regulatory requirements. The ability to target both fine and coarse particles ensures that hybrid systems can handle even the most challenging emission control scenarios.
Connect with us Now
How Intensiv-Filter Himenviro is Leading the Way in Hybrid Filtration Technologies
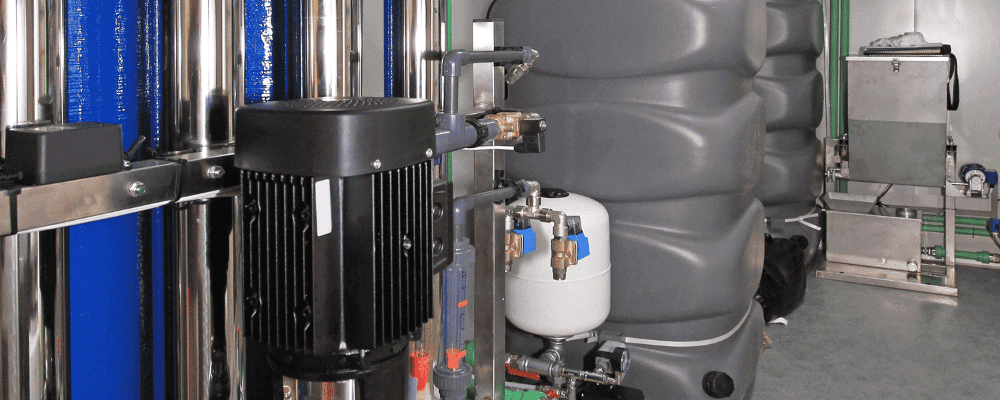
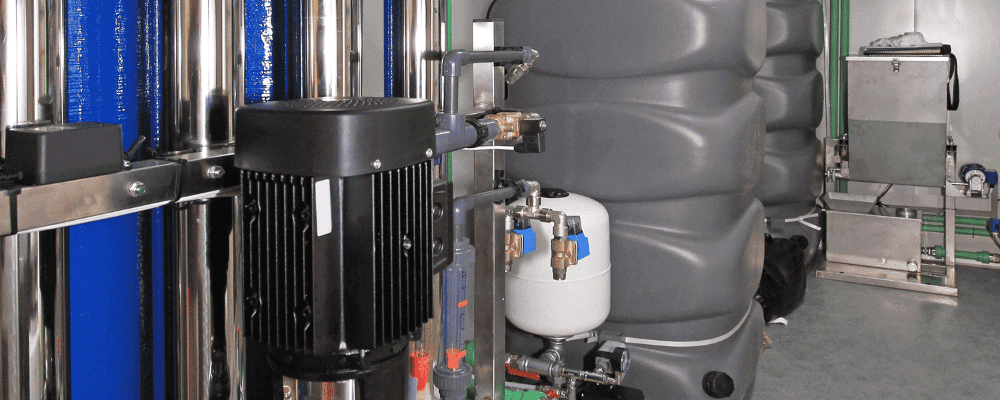
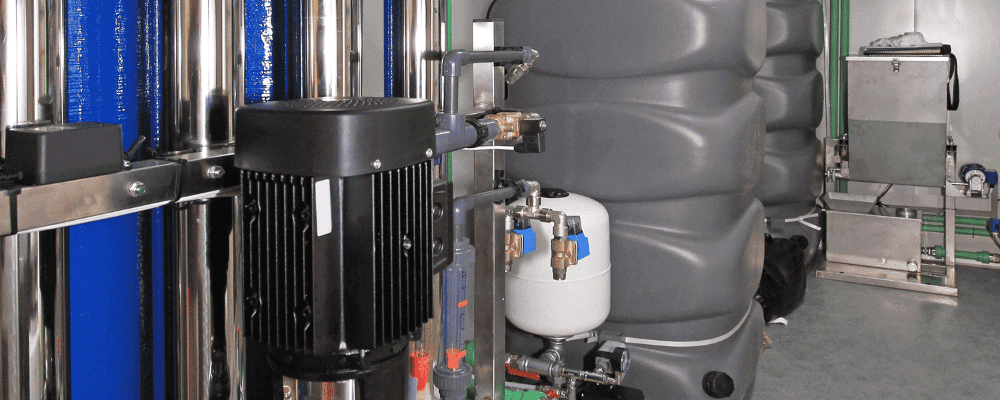
Intensiv-Filter Himenviro, a global leader in filtration technology, has recognized the growing demand for more efficient and reliable air pollution control systems. With decades of experience in industrial filtration solutions, the company has developed state-of-the-art hybrid filtration technologies designed to meet the needs of modern industries. Intensiv-Filter Himenviro’s hybrid filtration systems seamlessly integrate electrostatic precipitation with mechanical filtration, delivering superior air quality while addressing the specific challenges faced by industries that generate particulate emissions.
Customization and Flexibility
One of the hallmarks of Intensiv-Filter Himenviro’s hybrid systems is their flexibility and customization. Recognizing that no two industrial processes are alike, the company offers tailored solutions to meet the specific needs of each client. This customization extends to:
- Filter Media Selection: Intensiv-Filter Himenviro ensures that the mechanical filtration stage uses the most suitable filter media for the specific application, whether it’s woven, non-woven, or felted fabrics, depending on the temperature, chemical composition, and particulate load of the gas stream.
- Design Optimization: The company engineers its hybrid systems to handle a wide range of gas flow rates and particle sizes, ensuring peak performance across diverse industrial applications. This includes optimizing the dimensions of the ESP section and the mechanical filter to match the operational needs of the client.
- Energy Efficiency: Through its focus on reducing pressure drop and optimizing airflow, Intensiv-Filter Himenviro’s hybrid systems are designed to minimize energy consumption. By allowing the ESP section to remove a significant portion of fine particulates, the company ensures that the mechanical filter operates with a lower particulate load, resulting in less energy-intensive operation.
Industry-Specific Solutions
Intensiv-Filter Himenviro caters to a wide range of industries that face complex air pollution control challenges. The company has developed solutions that are adaptable to various industrial environments, including:
- Cement Industry: Cement production is one of the most dust-intensive industries, and hybrid filtration systems play a crucial role in reducing particulate emissions. Intensiv-Filter Himenviro’s hybrid systems are designed to handle the high-temperature exhaust gases and the varied particle sizes typical of cement production, capturing both fine and coarse dust with ease.
- Power Generation: In coal-fired power plants, hybrid systems developed by Intensiv-Filter Himenviro can significantly reduce particulate emissions by efficiently capturing fly ash and other particulates before they are released into the atmosphere. This helps power plants meet stringent environmental regulations while improving overall operational efficiency.
- Steel and Metal Production: Steel plants emit large volumes of dust and fine particles. Intensiv-Filter Himenviro’s hybrid systems are engineered to withstand high temperatures and corrosive environments while delivering top-tier particulate removal, helping metal producers meet regulatory standards.
- Pharmaceutical and Chemical Industries: Emissions from chemical and pharmaceutical plants often contain hazardous fine particles. Intensiv-Filter Himenviro’s hybrid filtration technologies are specially designed to capture these fine particulates, ensuring a safer working environment and cleaner emissions.
- Waste Management: Intensiv-Filter Himenviro provides solutions for waste incineration plants, where mixed emissions pose a significant challenge. The company’s hybrid systems effectively remove particulate matter from flue gases, helping waste management facilities achieve better environmental compliance.
Continuous Innovation
At Intensiv-Filter Himenviro, innovation drives the development of new filtration solutions. The company constantly invests in research and development to refine its hybrid filtration systems. This includes:
Advanced Monitoring and Control Systems: Intensiv-Filter Himenviro’s hybrid systems come equipped with smart monitoring tools that allow for real-time data collection and analysis. This ensures optimal performance, with automated alerts and adjustments to maintain peak efficiency.
Durable Materials for Longevity: The company uses high-quality materials for both ESP and mechanical filtration components, ensuring long-lasting performance even in the harshest industrial environments. This focus on durability helps reduce maintenance costs and extends the life of the system.
Focus on Sustainability: Intensiv-Filter Himenviro is committed to sustainability, and its hybrid filtration systems are designed to support cleaner air quality while minimizing resource use. By optimizing energy efficiency and reducing the need for frequent maintenance, the company’s systems contribute to lower operational costs and environmental impact.
Konklusyon
Intensiv-Filter Himenviro has established itself as a leader in the development and implementation of hybrid filtration technologies, providing industries with an effective and efficient solution for particulate control. By merging the strengths of ESPs and mechanical filters, the company’s hybrid systems offer unmatched air quality, operational flexibility, and cost savings across a wide range of applications.
As the industrial landscape continues to evolve and environmental regulations become stricter, hybrid filtration technologies represent the future of air pollution control. Intensiv-Filter Himenviro is well-positioned to lead this charge, delivering innovative solutions that help industries meet their emissions targets while improving overall performance.
With a commitment to continuous innovation, sustainable practices, and superior customer support, Intensiv-Filter Himenviro’s hybrid filtration systems stand out as a reliable and effective choice for industries seeking optimal air quality and operational efficiency.
Hybrid filtration technologies offer a compelling solution to the challenges of air pollution control across various industries. By merging the strengths of ESPs and mechanical filters, these systems provide enhanced efficiency, reduced maintenance, and improved adaptability to different operating conditions. Their ability to target both fine and coarse particles ensures optimal particulate removal, contributing to cleaner air and improved environmental compliance.
As industries continue to seek more effective ways to manage particulate emissions, hybrid filtration technologies are poised to become an increasingly important tool in the pursuit of optimal air quality. Whether in cement production, power generation, metal processing, or other industrial applications, these