Chemical production facilities are inherently susceptible to dust generation. From the processing of raw materials like limestone or phosphates to the final product itself, various stages contribute to a dusty environment. These dust particles pose significant safety and operational risks, demanding a robust and efficient dust collection system.
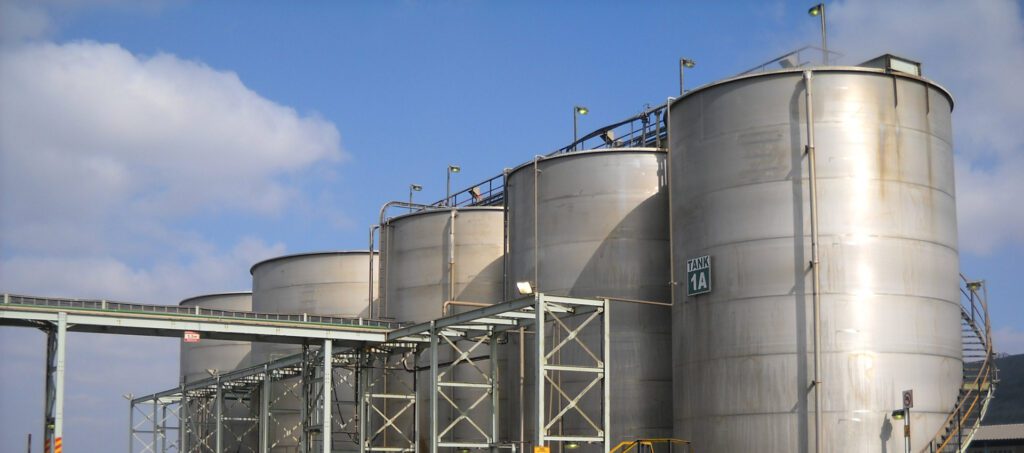
- Ineffectual Capture: Over time, dust collection systems become less effective due to filter wear and tear, leading to increased dust emissions. This meant that the existing system was no longer capturing all the dust particles generated during production. As a result, dust levels in the facility rose, exceeding safe limits.
- Safety Concerns and Explosion Risks: Chemical dust explosions are a major concern in these environments. Certain chemicals, when mixed with air in the presence of an ignition source, can create a highly volatile situation. Dust particles act as fuel, and their increased presence due to inadequate capture significantly amplifies the explosion risk. This posed a constant threat to employee safety and the integrity of the facility itself.
- Operational Inefficiencies: Dust accumulation on equipment and surfaces can disrupt production processes and hinder equipment performance. Frequent cleaning and system maintenance were necessary to maintain functionality, leading to production downtime and reduced efficiency. This not only impacted production output but also increased operational costs.
- Health Risks for Workers: Chronic exposure to airborne dust can have a detrimental impact on worker health. Depending on the specific chemicals involved, dust particles can irritate the respiratory system, causing coughing, wheezing, and long-term lung damage. Inhaling hazardous dust can also lead to more serious health problems like silicosis, a debilitating lung disease.
- Environmental Impact: Uncontrolled dust emissions can also have a negative impact on the surrounding environment. Dust particles can settle on nearby communities and vegetation, potentially affecting air quality and contributing to respiratory problems for people living in the vicinity.
Assessing the Situation: Comprehensive Approach to a Complex Problem
Intensiv-Filter Himenviro recognized the urgency of addressing these challenges. Here’s how we approached the situation:
- On-Site Visit and Detailed Inspection: Our team conducted a thorough site visit to the chemical manufacturer’s facility. This included a comprehensive inspection of the existing dust collection system, production processes, and dust generation points. The inspection focused on identifying the type of dust being generated, its source points, and the limitations of the existing system.
- Risk Assessment and Explosion Mapping: We conducted a detailed risk assessment, analyzing the various dust-related hazards present in the facility. This involved identifying specific chemicals with high explosion potential and mapping out potential ignition sources. This information played a crucial role in designing a new system that prioritized safety and minimized explosion risks.
- Data Collection and Analysis: We collected a range of data points to gain a comprehensive understanding of the dust control challenges. This included dust concentration levels in different areas of the facility, production volume, and performance metrics of the current system. By analyzing this data, we identified areas where improvements were most needed and determined the optimal capacity for the new dust collection system.
- Open Communication and Collaboration: Maintaining open communication with the manufacturer was paramount. This involved conducting collaborative meetings with key personnel to understand their specific needs, concerns, and budget limitations. We discussed their desired outcomes for the new system and ensured that our solution was tailored to their unique operational context.
By taking a comprehensive approach to assessing the situation, Intensiv-Filter Himenviro was able to create a customized dust collection solution that effectively addressed the leading chemical manufacturer’s challenges.
Tailoring a Solution: Addressing Specific Needs for Dust Control
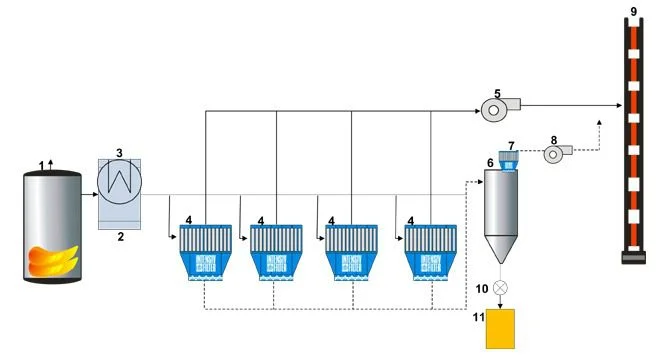
1. Prioritizing Safety: ATEX Compliance
- ATEX (ATmosphères EXplosibles) Certification: Knowing the manufacturer handled chemicals with explosion potential, we prioritized safety. The new system was designed and certified to meet ATEX standards. This ensures the system is built with explosion prevention features such as spark arrestors, pressure relief valves, and proper grounding to minimize explosion risks.
- Explosion Isolation and Venting: The system was designed with compartmentalization and explosion isolation features. This allows the containment of an explosion within a specific section of the system, preventing it from propagating and causing further damage. Additionally, explosion venting channels were incorporated to safely release pressure in the event of an incident.
2. Maximizing Efficiency: High-Performance Filtration
- Filter Selection for Specific Dust: Not all dust is created equal. We analyzed the specific characteristics of the dust generated in the facility (size, weight, chemical composition). Based on this analysis, we selected high-performance filters specifically designed for capturing this type of dust. This ensures optimal efficiency and minimizes the risk of filter clogging or breakthrough.
- Multi-Stage Filtration: For particularly challenging dust environments, the system may incorporate a multi-stage filtration process. This involves using multiple filters with varying degrees of fineness, progressively capturing larger and smaller particles. This ensures that even the most miniscule dust particles are effectively captured and removed from the air.
3. Adaptability for Future Growth: Modular Design
- The chemical industry is constantly evolving, and production needs can change over time. To ensure the system’s longevity and adaptability, we designed it with a modular approach. This allows for easy expansion and modification in the future. Additional modules can be seamlessly integrated into the system as the manufacturer’s production volume or dust generation points increase.
4. Automation for Enhanced Efficiency:
- Automated Controls and Monitoring: Manual monitoring of dust collection systems can be time-consuming and prone to human error. We incorporated automated controls and monitoring systems into the new design. These systems continuously monitor dust levels, filter performance, and system operation. Alerts can be triggered when parameters deviate from optimal levels, allowing for proactive maintenance and minimizing downtime.
- Self-Cleaning Mechanisms: To reduce maintenance requirements and improve efficiency, the system may include self-cleaning mechanisms for the filters. These mechanisms can use compressed air pulses or other methods to dislodge accumulated dust, ensuring optimal filter performance and extending filter life.
Implementing an Advanced Dust Collection System: Seamless Integration
We worked closely with the chemical manufacturer to seamlessly integrate the new dust collection system into their existing facility. Here’s how we ensured a smooth implementation process:
- Pre-Installation Planning and Coordination: Before any equipment arrived on-site, we meticulously planned for the installation process. This included detailed scheduling, coordination with the manufacturer’s team, and ensuring that the necessary space and resources were available for installation.
- Expert Installation and Commissioning: Our experienced technicians handled the entire installation process. This included installing all system components, connecting ductwork, and ensuring proper electrical and control system integration. Following installation, we commissioned the system, verifying its functionality and performing necessary adjustments.
- Comprehensive Training and Ongoing Support: We prioritize user knowledge and empowerment. We provided comprehensive training to the manufacturer’s personnel on the operation and maintenance procedures for the new system. This included both classroom-based training and hands-on experience to ensure they are comfortable operating the system effectively. Additionally, We offers ongoing technical support to ensure the system’s continued optimal performance.
By tailoring a solution to the specific needs of the leading chemical manufacturer and implementing it seamlessly, We delivered a dust collection system that revolutionized their approach to dust control.
Quantifiable Results: Enhanced Efficiency and Safety For Dust Control
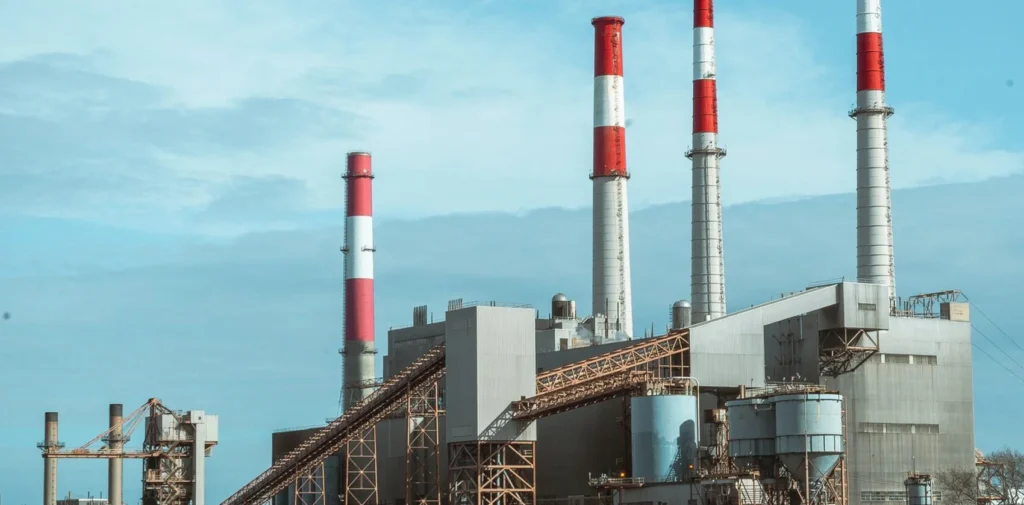
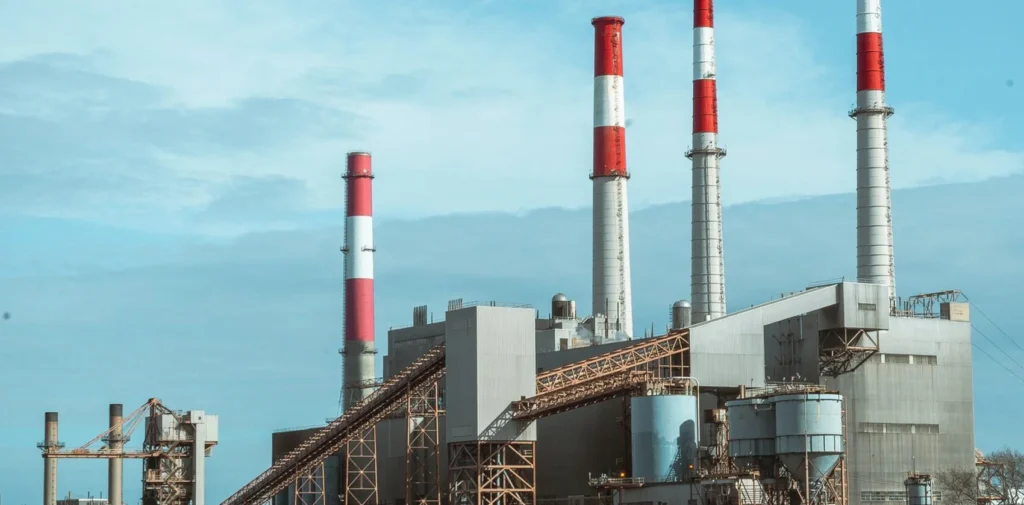
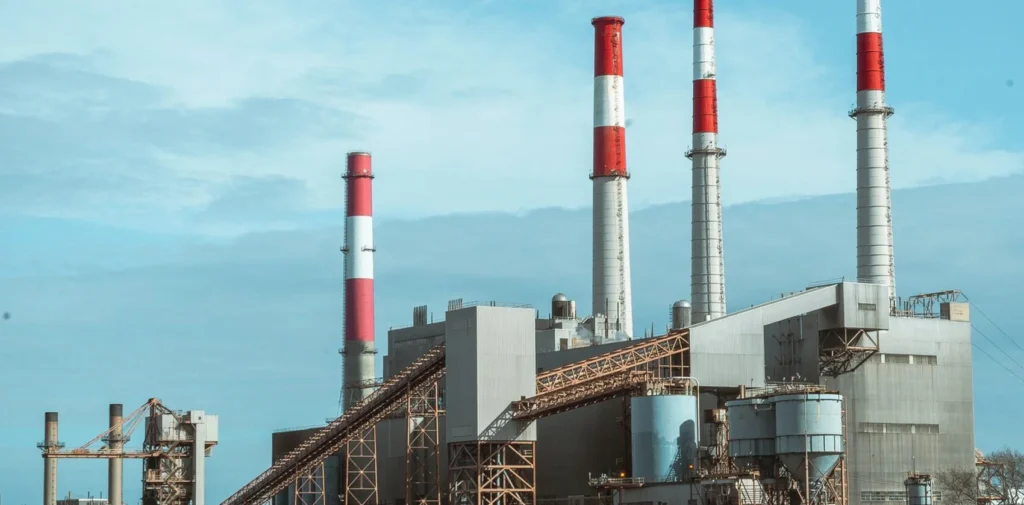
The implementation of the custom-built dust collection system by Intensiv-Filter Himenviro yielded significant and quantifiable results for the leading chemical manufacturer. Here’s a closer look at the positive impact across various aspects of their operations :
1. Dramatically Reduced Dust Emissions:
With the high-performance filters capturing a wider range of dust particle sizes, the new system dramatically reduced dust levels throughout the production facility. This was measured by utilizing dust monitors strategically placed throughout the plant. The reduction in dust emissions translated to:
- Improved Air Quality: Lower dust concentrations in the air created a healthier and safer working environment for employees. This reduces respiratory irritation and potential long-term health problems associated with chronic dust exposure.
Enhanced Visibility: Reduced dust levels improved visibility within the facility, leading to a safer work environment. This minimizes the risk of accidents due to obstructed vision.
Reduced Product Contamination: Lower dust levels also minimized the risk of product contamination during production, ensuring product quality and consistency.
2. Enhanced Safety and Explosion Prevention:
The ATEX-compliant system prioritized safety by minimizing the risk of dust explosions. Here’s how it achieved this:
- Reduced Explosion Risk: By effectively capturing dust particles, the system significantly reduced the potential fuel source for explosions. Additionally, the explosion isolation and venting features further minimized the consequences of any potential incident.
- Improved Worker Safety: Reduced dust explosion risks lessened the chance of employee injuries during production. This not only improved worker safety but also reduced the potential for costly downtime due to accident investigations and repairs.
3. Increased Production Efficiency:
The new dust collection system also delivered significant improvements in production efficiency. This was achieved through several factors:
- Reduced Maintenance Needs: Automated controls and self-cleaning mechanisms significantly reduced the need for manual cleaning and maintenance of the system. This freed up personnel for other tasks and minimized production downtime.
- Improved System Performance: The high-efficiency filters and automated controls ensured optimal system performance, maximizing dust capture and minimizing pressure drops within the system. This resulted in smoother and more efficient production processes.
- Reduced Cleaning Time: With less dust accumulation on equipment and surfaces, the time required for cleaning the production facility was significantly reduced. This freed up valuable production time and increased overall throughput.
4. Measurable Cost Savings:
The combined benefits of reduced maintenance, improved production efficiency, and minimized downtime translated into measurable cost savings for the chemical manufacturer. Additionally, the improved air quality within the facility minimizes the potential for health-related costs associated with dust exposure. These cost savings can be quantified and directly linked to the implementation of the new dust collection system.
Successful Partnership: Transforming Dust Control
The collaboration between Intensiv-Filter Himenviro and the leading chemical manufacturer exemplifies a successful partnership that transformed their approach to dust control. Here’s what contributed to this success:
- Understanding Client Needs: By prioritizing a comprehensive assessment and open communication with the manufacturer, we designed a system that specifically addressed their unique challenges.
- Expertise and Innovation: Our team’s expertise in advanced dust collection technologies allowed us to implement innovative solutions like ATEX compliance and multi-stage filtration.
- Seamless Implementation: The meticulous planning, coordination, and training ensured a smooth installation and transition to the new system.
- Ongoing Support: We recognize the importance of continued support and offer ongoing technical assistance to ensure the system’s optimal performance for years to come.
The positive outcomes achieved through this successful partnership demonstrate the transformative potential of effective dust control solutions. By partnering with Intensiv-Filter Himenviro, the leading chemical manufacturer not only improved safety and efficiency but also secured a more sustainable and environmentally friendly production environment.
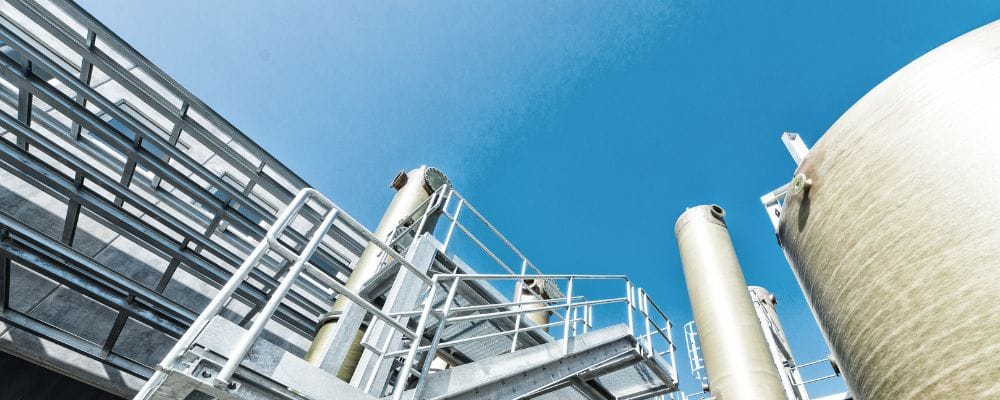
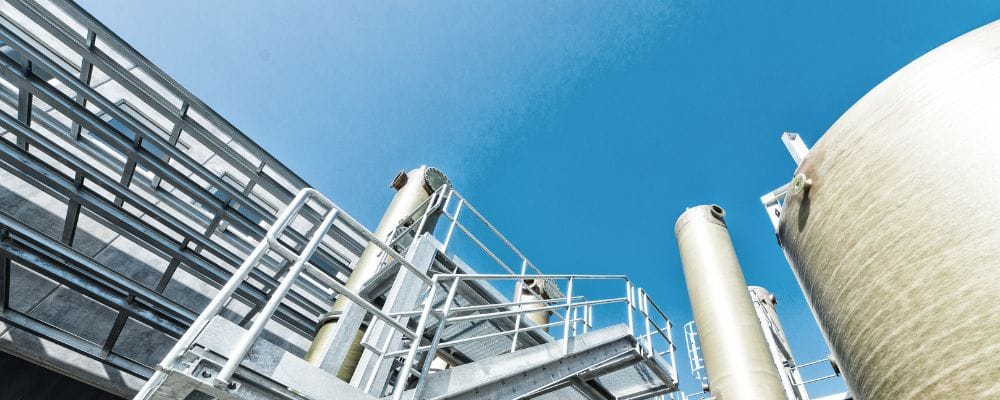
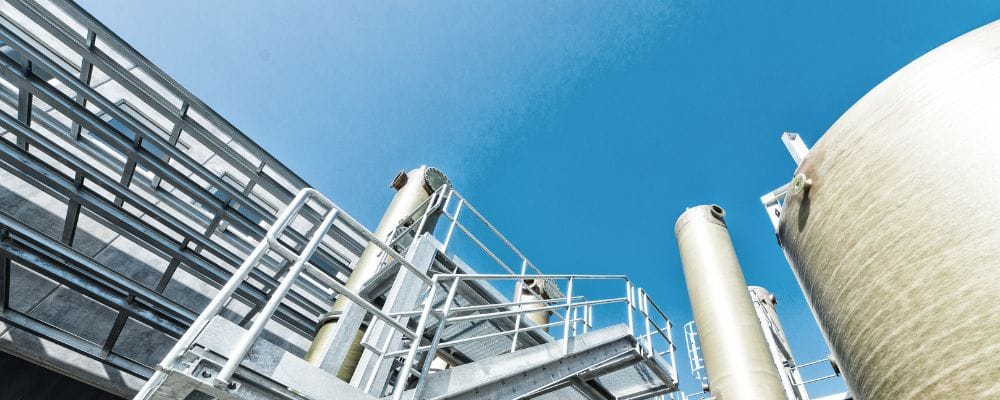
A chemical manufacturer had issues with their dust collection system, leading to safety hazards, health risks, and operational inefficiencies. Intensiv-Filter Himenviro assessed the situation, designed a custom solution with high-performance filtration and explosion prevention features, and implemented it seamlessly. The new system resulted in reduced dust emissions, improved safety, increased production efficiency, and cost savings.