Industrial Bag Filter Solutions
The Bag Filter is an advanced dust collection system designed to efficiently capture particulate matter from industrial processes, ensuring a cleaner and safer environment. It works through a continuous, automatic bag cleaning mechanism using periodic bursts of compressed air. These bursts create a pneumatic shock that dislodges dust particles from the filter bags, allowing for uninterrupted airflow while keeping the system operating at peak efficiency. This innovative dust control solution is particularly effective in industries with high dust and particulate emissions, including cement, steel, textiles, sugar, woodworking, and more.
The Bag Filter is engineered for high-performance filtration and designed to handle dust generated during crushing, grinding, transportation, and other heavy industrial processes. It is customizable to meet the specific needs of various applications, offering durability, energy efficiency, and ease of maintenance. The system ensures compliance with stringent environmental regulations and worker safety standards, making it an essential solution for industries looking to improve air quality and reduce operational disruptions.
Operational Benefits of Bag Filters
Dust collection system begins with the entry of dust-laden air into the collector, either through a hopper or casing. As the air enters, an internal baffle distributes it evenly within the housing, allowing for efficient filtration. As the airflow slows down, coarser dust particles settle into the hopper. The remaining air, carrying finer dust particles, passes through filter bags where the dust is captured on the exterior surface. Clean air then flows to the clean air chamber and is exhausted to the atmosphere. To maintain optimal performance, a periodic pulse of compressed air is used to dislodge the accumulated dust from the filter bags. The dislodged dust falls into the hopper for collection and disposal. The frequency and duration of the cleaning cycles are precisely controlled by solid-state timers or programmable logic controllers (PLCs).
Dust Collection Process
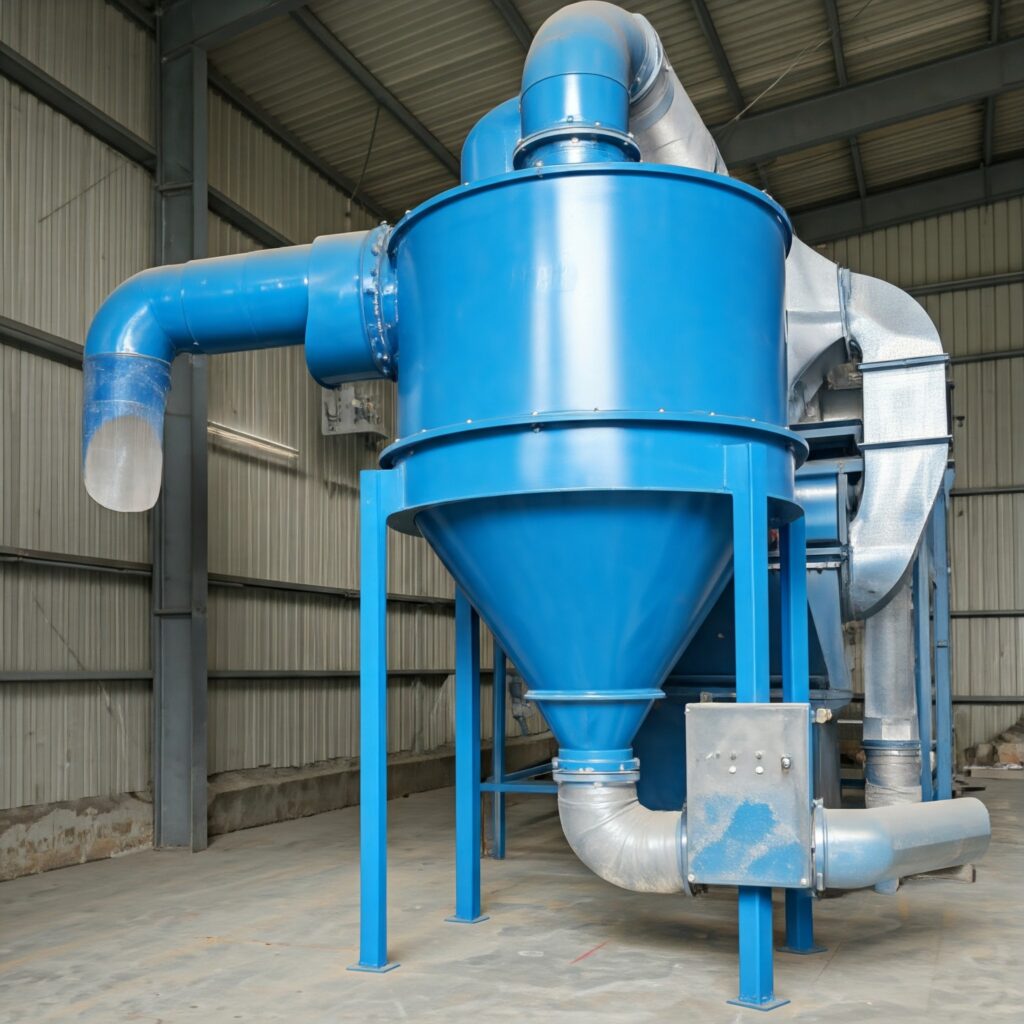
Dust-laden air enters the dust collector via the hopper or casing, depending on the specific application.
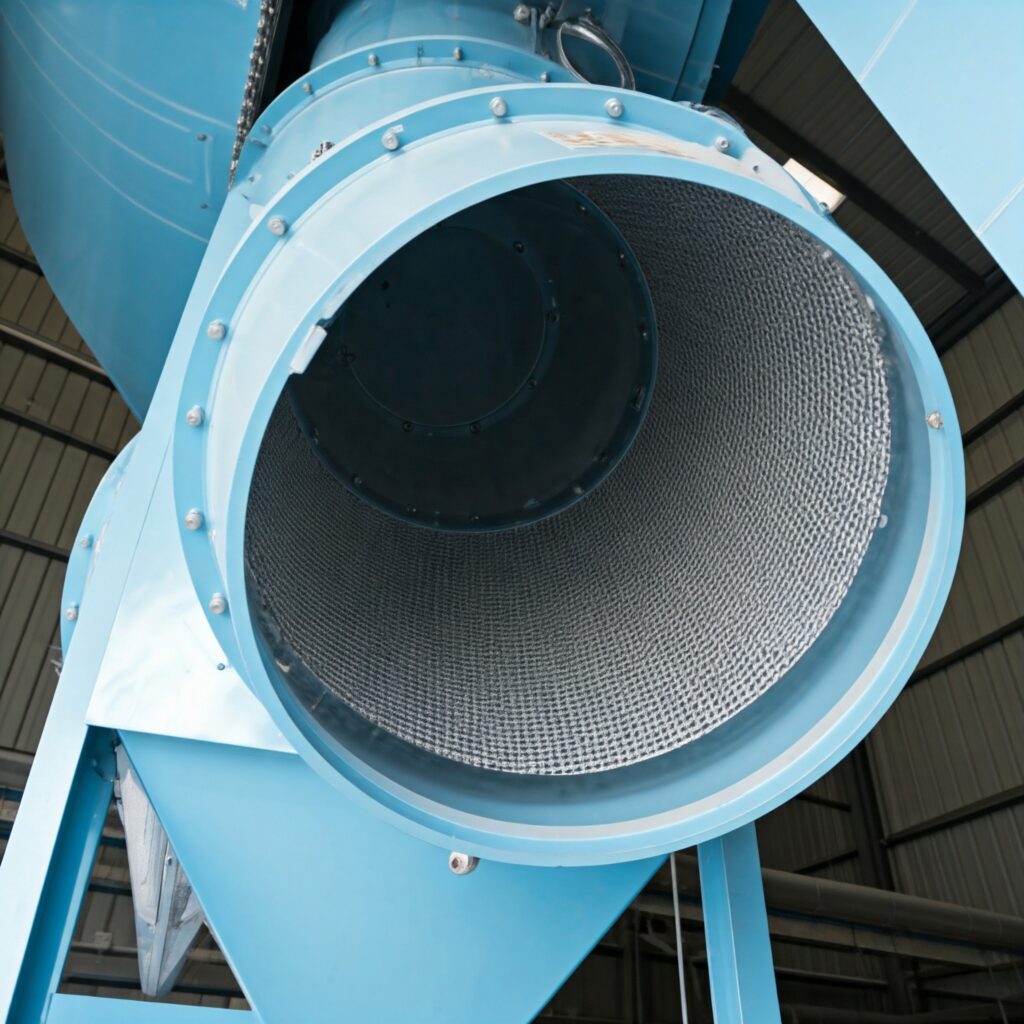
The air is distributed within the collector by an internal baffle, and dust particles are trapped on the exterior of the filter bags.
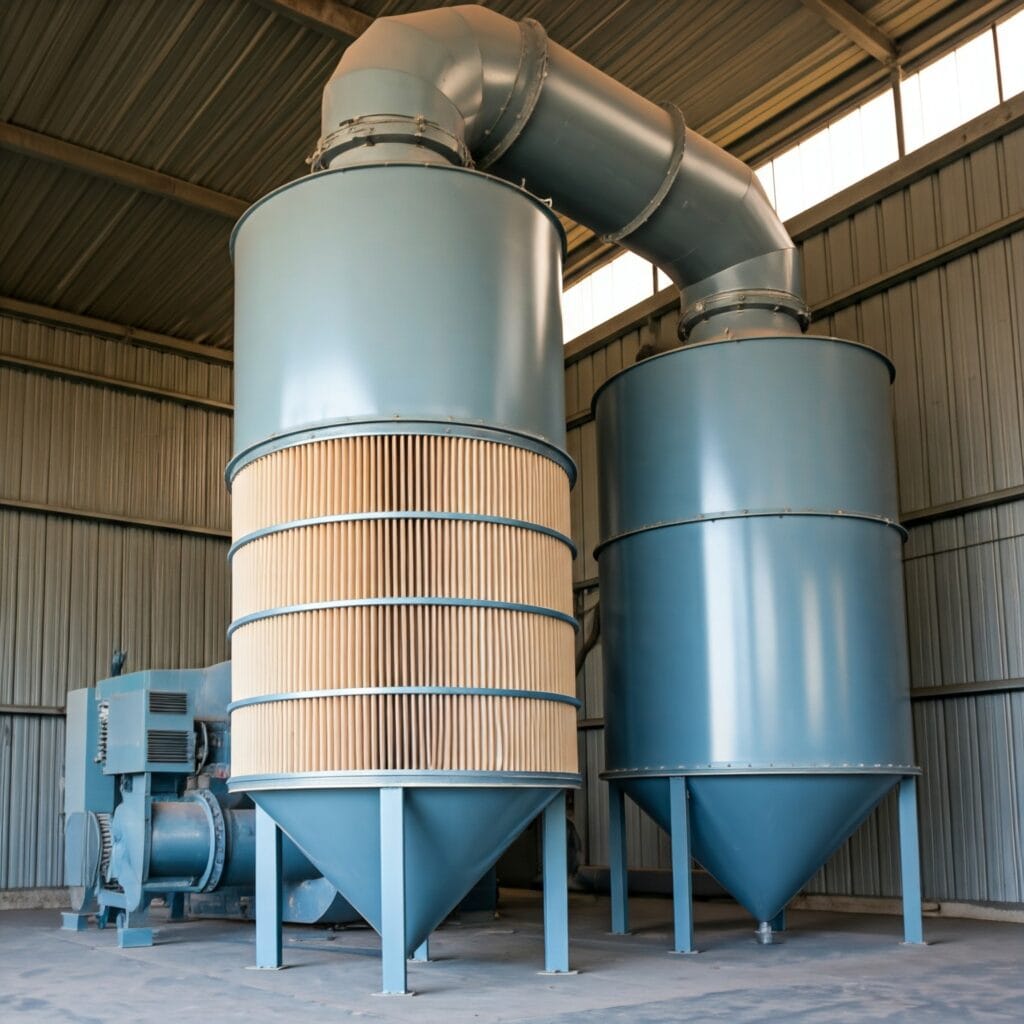
The clean air flows through the bags into the clean air chamber, where it is expelled through the exhaust outlet.
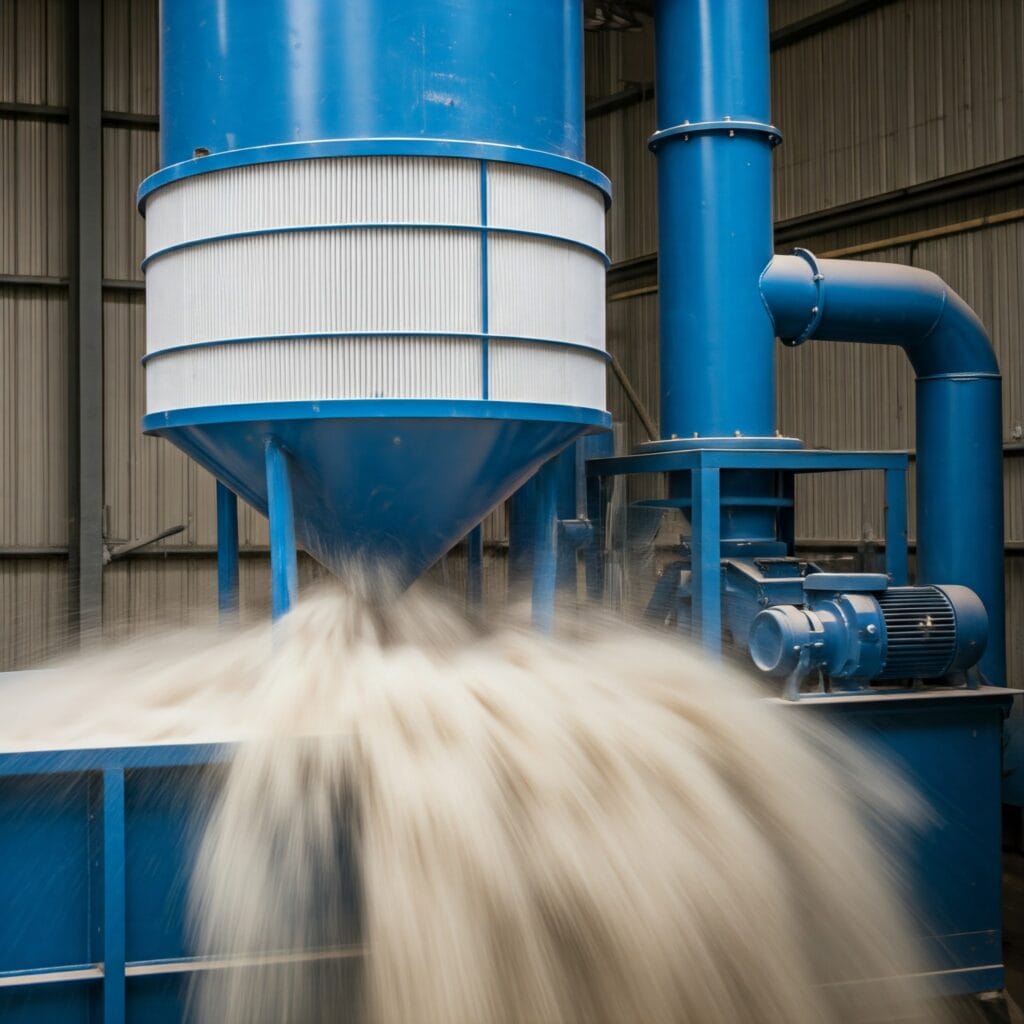
Periodically, compressed air pulses are directed down through the bags, causing the accumulated dust to be dislodged.
Applications for Fabric Filter
|
---|
Cement & Mineral Industries
|
Steel Production
|
Textile Industry
|
Sugar Industry
|
Wood working
|
Coal & Fly Ash
|
Food Processing
|
Pharmaceutical Manufacturing
|
Chemical Processing
|
Key Features and Benefits
|
---|
Continuous Operation
|
Energy Efficiency
|
Ease of Installation
|
Low Maintenance
|
Quick Bag Replacement
|
Reduced Operational Costs
|
Improved Air Quality
|
Increased Bag Life
|
Versatile Application
|
Advantages
|
---|
Efficient Dust Control
|
Low Energy Consumption
|
Simplified Installation
|
Durability
|
Safety Compliance
|
Minimal Downtime
|
Reduced Environmental Impact
|
Cost-Effective
|
Adaptable to Various Industries
|
Connect with us for Expert Consultation
Explore Our Other Services !
Frequently Asked Questions
Fabric filters are commonly made from materials such as polyester, polypropylene, aramid (Nomex), fiberglass, and PTFE (Teflon). These materials are chosen based on their durability, temperature resistance, and chemical compatibility. Polyester is widely used for general applications, while aramid and fiberglass are preferred for high-temperature environments. PTFE provides excellent chemical resistance and is used in highly corrosive conditions. The selection of material depends on the specific industrial requirements and operating conditions.
Common challenges in fabric filter operation include clogging due to excessive dust accumulation, which reduces airflow and efficiency. High operating temperatures can degrade filter materials, shortening their lifespan. Moisture in the gas stream can cause filter blinding, making cleaning difficult. Chemical exposure may lead to fabric deterioration, affecting performance. Improper cleaning cycles can result in excessive wear or inefficient dust removal. Regular maintenance, proper material selection, and optimized cleaning systems help mitigate these challenges.
Fabric filters enhance operational efficiency by providing high dust collection efficiency, ensuring cleaner air and reducing equipment wear. They help maintain stable airflow, preventing blockages and pressure drops that can disrupt production. By capturing and recovering valuable particulate matter, they reduce material waste and improve resource utilization. Additionally, effective filtration minimizes maintenance needs, lowers energy consumption, and ensures compliance with environmental regulations, leading to smoother and more cost-effective operations.
Case Study
Read Related Case Studies