Industrial dust poses a significant threat to both air quality and worker health. Imagine a factory floor filled with airborne particles, reducing visibility, compromising product quality, and putting workers at risk of respiratory illnesses. Here’s where fabric filters step in, acting as the guardians of clean air in industrial dust collection systems. By capturing these airborne particles, they ensure clean air emissions and a safer work environment. This post delves into the world of fabric filter media, exploring the different types, selection criteria, and their diverse applications across industries.
The Fabric Filter Media Landscape: Woven vs. Non-Woven
Fabric filter media comes in two main categories, each with its own strengths and ideal applications:
1. Woven Fabrics: Resembling a tightly woven tapestry, woven fabrics excel in:
- Dimensional Stability: Their strong, interlaced structure maintains shape even under pressure, ensuring consistent filtration performance over time. This is crucial for applications requiring continuous and reliable dust capture.
- High Filtration Efficiency: The tight weave effectively traps fine particles, making them ideal for capturing hazardous or very small dust particles that could pose a health risk or compromise product quality.
Common Woven Fabric Materials:
- Cotton: Affordable and readily available, offering good chemical resistance in dry environments. However, it’s susceptible to blinding (dust caking) by moisture or sticky dust and not ideal for high temperatures.
- Polyester: A popular choice due to its affordability, durability, and wider range of chemical and temperature resistance compared to cotton.
- Fiberglass: Effective for capturing fine particles at high temperatures due to its heat resistance. However, special handling is required due to potential health hazards associated with fine fiberglass fibers.
2. Non-Woven Fabrics: Formed by bonding fibers together, non-woven fabrics offer distinct advantages:
- High Dust Cake Release: The looser structure allows dust to detach easily, preventing blinding and maintaining good airflow. This is ideal for applications with sticky or cohesive dust that can cake on woven fabrics and hinder filtration efficiency.
- Lower Pressure Drop: Air flows through more easily compared to woven fabrics, potentially reducing energy consumption for the filtration system. This translates to lower operating costs.
Common Non-Woven Fabric Materials:
- Spunbond Polyester: A cost-effective option with good dust cake release properties and decent filtration efficiency
- Felt: Often used for its excellent cake release and ability to handle high airflow rates.
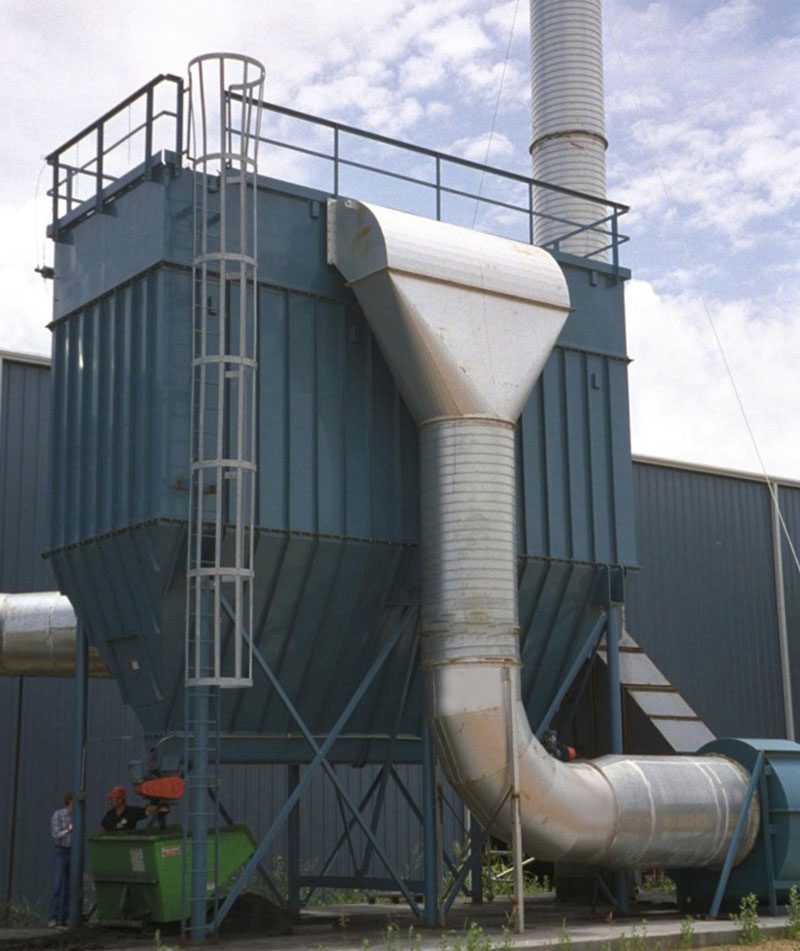
Choosing the Right Media: A Tailored Approach
- Dust Characteristics:
Size and Shape: Finer particles necessitate finer media for efficient capture.
Abrasiveness: Highly abrasive dust may require more robust media like fiberglass to withstand wear and tear.
Chemical Composition: Compatibility with dust chemicals is crucial to avoid degradation of the media.
- Operating Conditions:
Temperature: Ensure the media can withstand the dust-laden air stream’s temperature without melting or losing integrity.
Airflow Rate: Balance pressure drop with desired airflow for optimal energy consumption.
Beyond the Basics: Advanced Media Options
As technology advances, innovative fabric media options cater to specialized needs:
- Membrane Fabrics: A thin, microporous membrane laminated onto a base fabric. These offer superior filtration efficiency for submicron particles while maintaining good cake release properties.
- Anti-static Fabrics: Static cling can hinder dust release. These fabrics are treated with conductive materials to dissipate static charges and improve cleaning efficiency.
- Hydrophobic Fabrics: For applications with moisture-laden dust, these fabrics have a water-repellent coating to prevent blinding and maintain filter performance.
Choosing the Right Media: A Tailored Approach to Peak Performance
Selecting the optimal fabric media isn’t a one-size-fits-all approach. For your dust collection system to perform at its peak, several factors require careful consideration to ensure a perfect fit for your application. Here’s a breakdown of the key elements to consider:
Understanding Your Dust Enemy
- Size and Shape: Finer particles necessitate a finer media for efficient capture. Imagine a strainer – you wouldn’t use a large mesh to catch tiny grains of sand! The same principle applies to fabric filter media.
- Abrasiveness: Highly abrasive dust, like metal shavings, can wear down some media faster. More robust media, like fiberglass, might be necessary in such cases.
- Chemical Composition: Some dusts can react negatively with certain media materials, causing degradation. Knowing the chemical makeup of your dust is crucial to choosing compatible media that won’t break down.
Optimizing for Your Operating Environment
- Temperature: The media needs to withstand the temperature of the dust-laden air stream. For example, high-heat processes might require specialized media that won’t melt or lose integrity.
- Airflow Rate: Balancing pressure drop with desired airflow is key for optimal energy consumption. Tighter weave media might offer superior filtration but can restrict airflow, requiring more energy to push air through.
Cleaning Mechanism Compatibility
The type of cleaning mechanism used in your dust collection system can influence media selection:
- Pulse-jet systems offer more flexibility in media choice due to their powerful cleaning action.
- Reverse-air bag houses may require more open media structures for effective cleaning with their gentler approach.
Beyond the Basics: Advanced Media Options for Specialized Needs
As technology advances, innovative fabric media options cater to specific challenges:
- Membrane Fabrics: Imagine a microscopic mesh laminated onto a base fabric. These offer superior filtration efficiency for submicron particles, ideal for capturing ultra-fine dust.
- Anti-static Fabrics: Static cling can hinder dust release from the media. These fabrics are treated with conductive materials to dissipate static charges and improve cleaning efficiency.
- Hydrophobic Fabrics: For applications with moisture-laden dust, these fabrics have a water-repellent coating that prevents blinding and maintains filter performance.
Connect with us Now
Fabric Filters in Action: Safeguarding Air Quality Across Industries
The versatility of fabric filters makes them instrumental in maintaining clean air and worker safety in a wide range of industries:
- Food Processing: Fabric filters capture flour dust, sugar dust, and other airborne particles, protecting product quality and worker health from respiratory issues. Imagine breathing in flour dust all day – not pleasant!
- Pharmaceuticals: In pharmaceutical manufacturing, fabric filters help maintain cleanroom conditions by capturing potent drug particles and excipients, ensuring product sterility and regulatory compliance. Here, even the slightest contamination can have serious consequences.
- Woodworking: Wood dust is a health hazard and can be explosive. Fabric filters effectively remove sawdust and wood chips from workshop air, creating a safer and healthier work environment for woodworkers.
- Cement Production: Fabric filters play a critical role in capturing fine dust particles generated during cement manufacturing, significantly reducing air pollution. This helps cement plants be responsible environmental stewards.
- Metal Processing: Metalworking processes create dust and fumes. Fabric filters help control these emissions, protecting workers from exposure and complying with environmental regulations.
By understanding the different types of fabric filter media and their selection criteria, companies can optimize their dust collection systems for specific applications. This not only ensures clean air but also contributes to a safer and healthier work environment, and promotes environmental sustainability. It’s a win-win for everyone!
In conclusion, fabric filters are the unsung heroes of industrial air quality control. By understanding the various media options and selection criteria, companies can choose the right filter for their specific needs. This ensures clean air for workers, protects product quality, and promotes environmental responsibility. From food processing to metalworking, fabric filters play a vital role in creating a healthier and more sustainable future for us all.