In this reference plant at the steelworks of HKM, the existing extraction plant capacity was improved by a new bag filter. The original extraction air volume of ~ 700,000 m³/h was increased by an additional 600,000 m³/h with the new filter plant. The dust removal capacity from the torpedo ladle syphoning pit and hot-metal desulphurization could be improved significantly as a result.
The new Filter 5 was built in an open space opposite the steel works. Since then, the customer’s existing Filter 4 and the new Filter 5 have been running simultaneously. This guarantees effective dust removal for all the gases in the charging area and all other areas of the steel works.
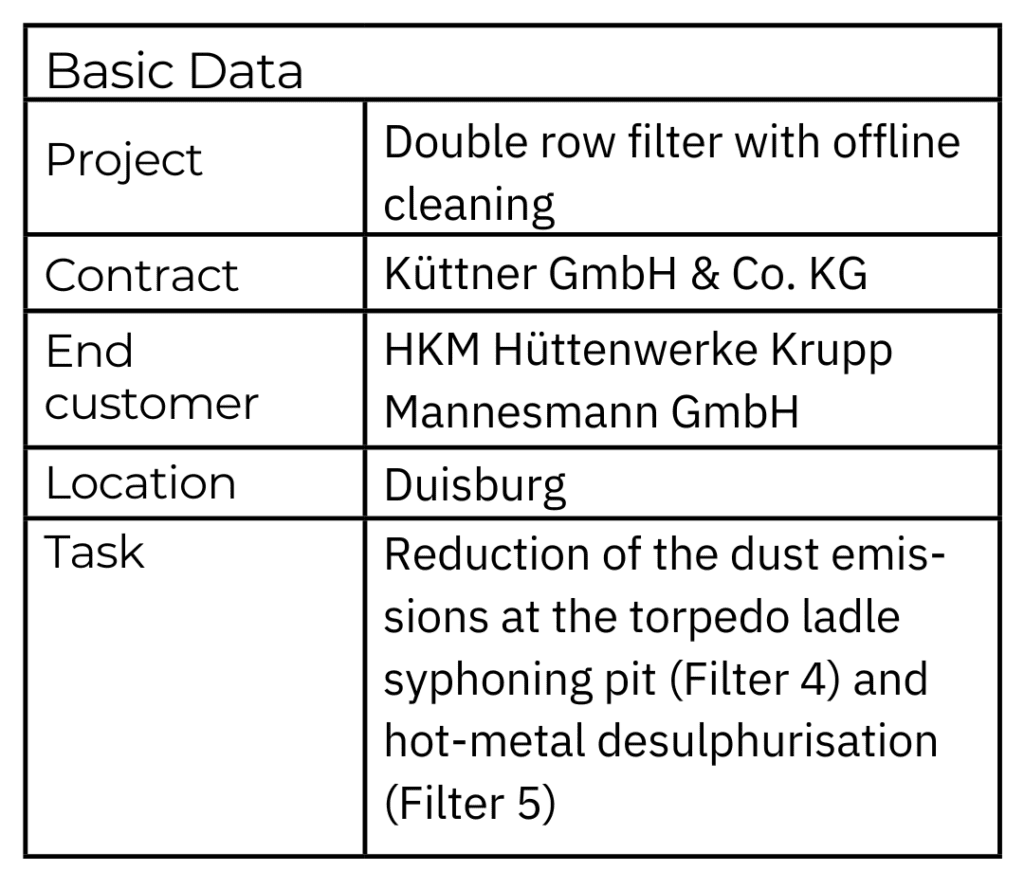
The CombiJet Bag Filter for the Steel Industry
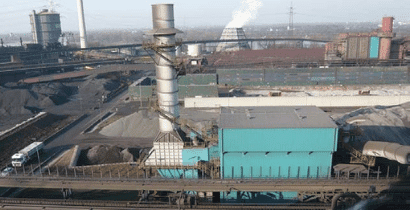
First Class Quality
Intensiv-Filter has carried out the dust removal and gas cleaning for the commitment of modern implementation changes at the steelworks. Based on the specific customer conditions, the dust removal represents a complex waste gas cleaning installation, which required the implementation of process engineering solutions.
The Patented Cleaning
For “offline“ cleaning, the filter chamber to be cleaned is isolated by closing the valve on the clean gas side. Cleaning is carried out by injecting compressed air in the opposite direction to the filtration flow via the two-stage “Coanda“ annular gap injector. A fan is used to channel the reverse air out of the clean gas flow to the individual compartments. This “offline“ cleaning ensures that fine dust is thoroughly channeled into the dust collection hopper, via a downward flow after the filter bags have been isolated. Once a filter compartment has been cleaned, the next filter compartment is switched into the cleaning sequence.
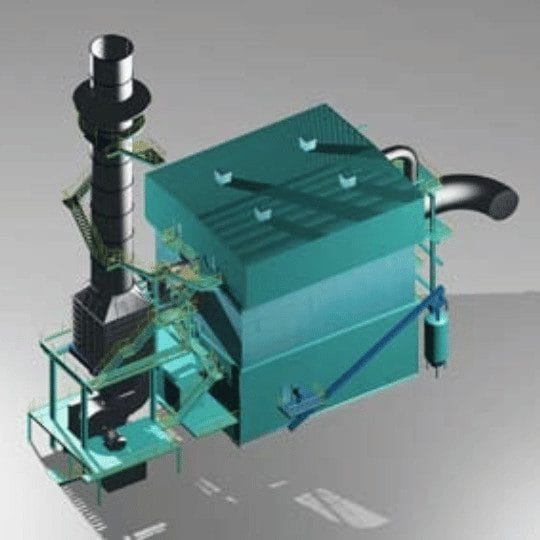
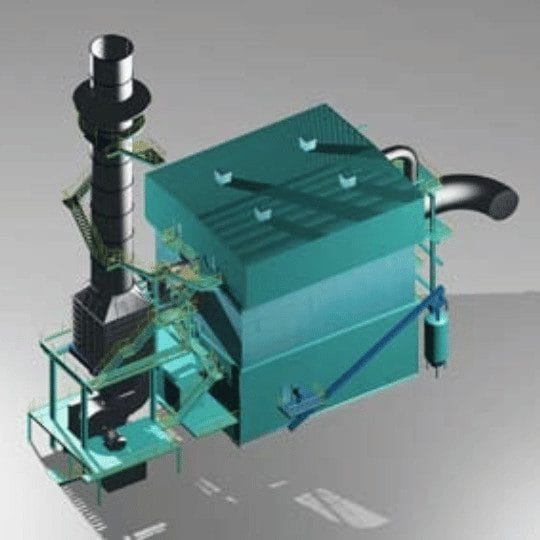
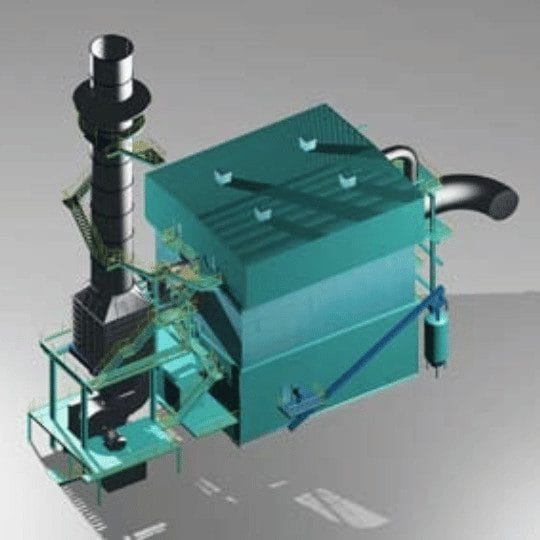
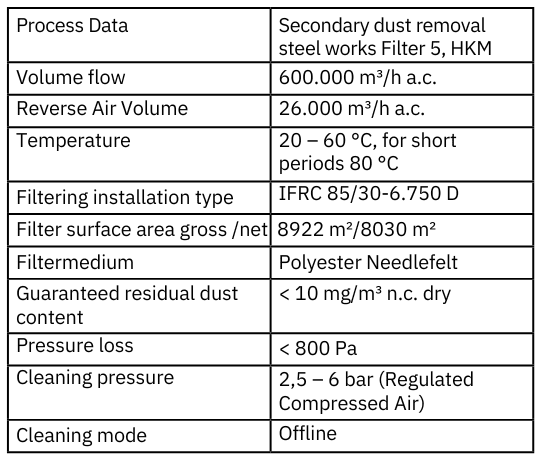
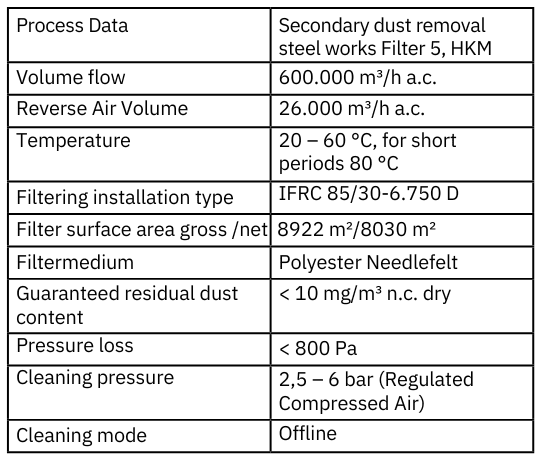
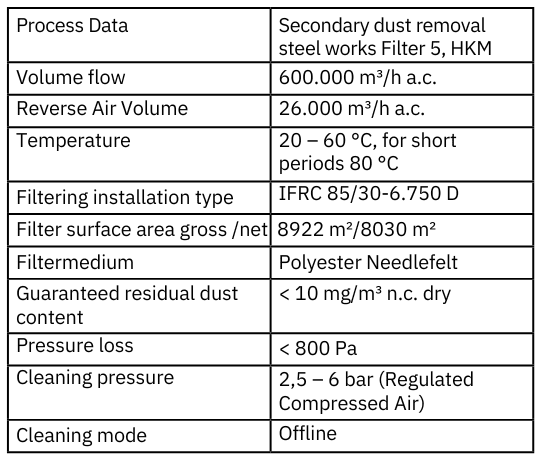
Constructive Design for the Dust Removal System
A two-row bag filter cleaned with compressed air was applied as a so called “double row filter“ in offline cleaning. The double filter has a compact design, with a combined raw and clean gas channel, which allowed a lot of space to be saved. The baffle plates and deflectors in the channel ensure that the raw gas flow is distributed evenly, and also reduces the wear on the filter bags by screening them and directing the flow.
Customer Benefit
- Reduction of the MAK-values at the work stations
- Clean gas dust emissions clearly within legal requirements
- Increased extraction power
- Better dust removal achieved by supply of secondary air in the cleaning phase
- Lower operating costs by reduced pressure drop across the filter due to offline cleaning
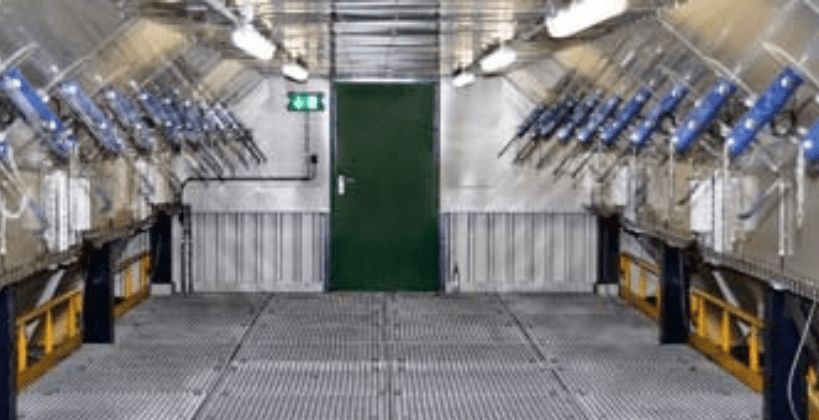
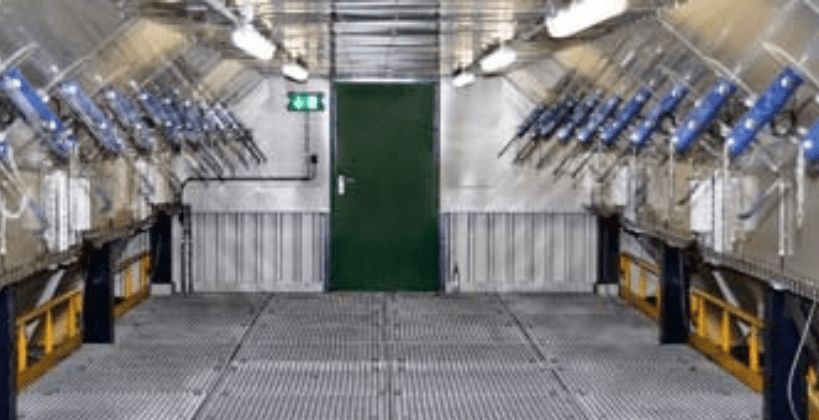
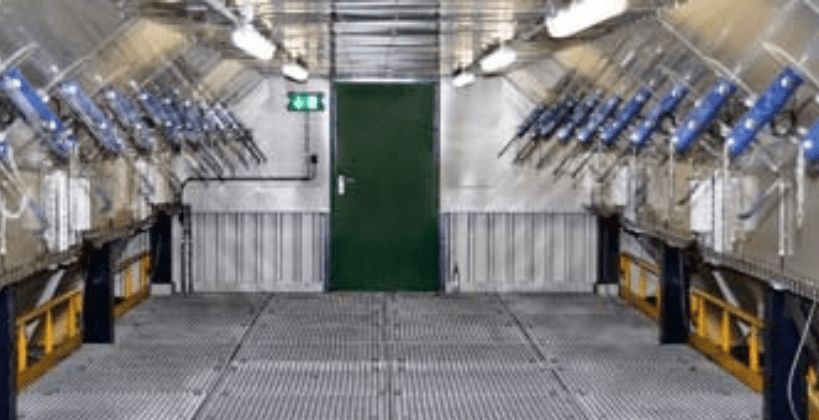
Filtering dusts is the task Intensiv-Filter Himeviro has been addressing itself to since its foundation in 1922. As a specialist in filtering installations we have a leading position in the international markets. This applies both to new installations and to conversions in various business areas.